Станки самодельный: Делаем самодельные станки и инструменты своими руками
Самодельные мини токарные станки по металлу
(Из книги Е. Васильева «Маленькие станки»)
Самоделкины из разных стран естественно не обошли вниманием и маленькие станочки. Вот несколько самодельных конструкций. В таких проектах обычно используются круглые шлифованные стержни в качестве направляющих, и потому такие конструкции часто напоминают легендарный Unimat DB/SL.
Пример самодельного станочка показан на фото (его основные корпусные детали изготовлены из алюминия).
В следующем токарном цыплёночке используется цанговый патрон с набором цанг от станка «Taig». На фото общий вид.
Дополнительные фото:
Передняя бабка,
Задняя бабка,
Шпиндель,
Суппорт
Цанги.
Как видим, простые в изготовлении круглые направляющие применяются во многих конструкциях. Но существует устойчивое мнение о слишком низкой жесткости такой конструкции. Возможно, это так, но у меня появилось подозрение — не миф ли это.
Может быть, направляющие и не виноваты во всех грехах, что им приписывают? Маленький станок любой конструкции, ну может за исключением промышленных станочков, имеет скромный запас жесткости. Например, я пользуюсь станками, где направляющие обычные, литые чугунные. И когда начинается свист и вибрация, я ищу причины в другом, подпираю деталь центром задней бабки, меняю режимы резания, меняю заточку резца и, в конце концов, нахожу какой-то приемлемый вариант и работаю. Но с проблемой низкой жесткости я и без круглых направляющих сталкиваюсь частенько. А вот если бы направляющие этих станочков были круглыми, возможно я бы пенял и плевался на них, не подозревая, что причина совсем не там.
Конечно, нет дыма без огня, но
Юниматы DB/SL по-прежнему народ покупает очень охотно.
Здесь описание и чертежи (http://www.chipmaker.ru/index.php?showtopic=211) этого самодельного станка. Ввиду дефицитности маленьких токарных патронов и их достаточно высокой стоимости, в станке применён сверлильный патрон вместо токарного.
Юрий Кимборович. Вид со стороны задней бабки
Юрий Кимборович. Привод Юрий Кимборович. Механизм подачи
С форума:
Ю.К.
Направляющие — стержни передних стоек амортизаторов ВАЗ 2109 диаметром 22 мм, со стороны тонкой резьбы обрезаны и проточены под стандартную резьбу М14х1,5, с другой стороны она уже есть.
Пришлось заказать корпус шпинделя, ось и заднюю опору для направляющих. Отверстия для направляющих и оси шпинделя делали с одной установки на координатке, от этого зависит точность. При сборке использовал прокладки из латунной фольги для установки направляющих. При следующих замерах выяснилось, что точность установки направляющих по оси шпинделя у задней опоры по горизонтали получилась 0,02 мм, по вертикали 0,05 мм. Для моих задач более чем нормально.
Для супорта использовал болванку с отверстием под втулки для передней направляющей. Болванка и втулки разрезаны и стянуты винтами для регулировки люфта. В задней отфрезерована ступенька, которой супорт опирается через латунную прокладку на заднюю направляющую. Снизу поджимается пластиной 3мм. На супорт сверху привинчен однокоординатный столик от какого-то оптического прибора. Выточил для него ходовой винт М6 латунную гайку и два упора практически вручную, сверху на столике прикручена 5 мм пластина и резцедержатель. Продольный ходовой винт из стандартной шпильки М12, их на строительных ранках продают, закреплен в латунных втулках на корпусе шпинделя и задней опоры.
Задняя бабка сделана из куска 70 мм уголка, 12 мм пластины, в которой профрезерован треугольный паз под переднюю направляющую, и ступенька под заднюю, а также отрезка 20 мм стержня. Все это сварено «на глазок» но желательно поточнее. Затем бабка устанавливается на свое место. Нижний поджим на бабке регулируется так, чтобы она перемещалась вдоль направляющих с достаточно большим усилием. В патрон шпинделя зажимается сверло небольшого диаметра (я начал с 4 мм) и перемещая бабку к шпинделю, потихонечку, аккуратно просверливается в ней продольное отверстие. Затем берётся сверло больше на 0,5мм. и операция повторяется. И так до диаметра 6,7 мм. Приличная соосность гарантируется. Затем, в патрон вставляется метчик М8, и поворачивая патрон воротком — нарезается резьба в задней бабке.
В принципе, вкратце все. Буду рад, если кому-то пригодится.
В задней бабке вращающегося центра у меня нет — когда нужно, использую каленый неподвижный центрик, который вставляется вместо сверла в цанговый патрончик задней бабки.
— Замечательная самоделка! На рынке видел токарные патроны диаметром 80 мм. Не влезет такой на Ваш станок?
Ю.К. — Насчет патрона — 80-й для него слишком большой и тяжелый. Когда-то советская промышленность для часовых станочков выпускала токарный патрон 60 мм и обозначался он С92. Видел такой на часовом станке, но найти такой раритет не удалось….
Чертежи сделаны до изготовления станка в довольно простом векторном редакторе Xara X. Просто мне когда-то пришлось много в нем поработать и работаю в нем довольно быстро. Оформлять пришлось так, чтобы было понятно тем, кому заказывал детали. А эскизы перерабатывались раз 15 в редакторе в поисках упрощения конструкции, прежде чем приступить к металлу. Что получилось сами видите.
В принципе, он у меня трудяга. Большой станок только купил и сейчас ремонтирую, а на этом вся мелочевка точится уже год. Вчера, кстати, для коробки передач большого станка на нем выточил десяток контровочных винтиков М6х8.
Если есть вопросы по конструкции — задавайте, буду рад ответить.
***
Кем-то начатая, но не доведённая до конца работа — самодельный токарный станочек (найден на даче). Возможно, ещё получит вторую жизнь, так как нашёл нового хозяина.
Ещё одна самоделка, на этот раз собрана из готовых узлов разных станочков. На мой взгляд, получилась неплохая конструкция — только мотор добавить, да станину поставить на ножки. Фотография взята с Металлического форума.
Посмотрите и эту ссылку:
http://www.osipoff.ru/dump/forum.php?forum=37
и на ней раздел «Станки самодельные». Там много примеров разных конструкций, подобных той, что на фото.
Правда, с тем, что там написано про двигатели с постоянными магнитами, мол, такие двигатели крутятся стабильно, и якобы обороты зависят только от напряжения, я не согласен. При разной нагрузке такие двигатели, конечно же, меняют и частоту вращения. И при использовании в станочках нуждаются в стабилизации оборотов.
Вообще весь сайт Андрея Осипова Электроника СТУДИЙНЫХ ВСПЫШЕК (http://www.osipoff.ru/) очень познавательный и интересный, причём именно этот сайт во многом послужил мне примером того, как можно сделать технический ресурс Интернета наглядным, интересным и информативным. Поэтому рекомендую его ресурс всем читателям, интересующимся не только станками, но, прежде всего, фотографией или электроникой.
Изготовить качественно узел шпинделя с подшипниками качения довольно сложно, но при не слишком больших нагрузках хорошо работают конические бронзовые втулки в сочетании со стальным шпинделем.
Для смазки таких втулок используются специальные маслёнки. Вот фото таких маслёнок на японском токарном Eguro и справа подобная маслёнка крупным планом.
Самодельный ЧПУ станок как собрать самому
Самодельный ЧПУ станок можно собрать самому
2017-09-12
Станок с ЧПУ у себя дома – не мечта, а реальность
Ныне обработка всевозможных материалов возможна не только на заводских цехах. Ранее домашние мастера максимум, что могли себе позволить, это выпиливание лобзиком. На сегодняшний день самодельный ЧПУ станок для резки ручного использования продаются в любом бытовом магазине. Линейная обработка выполняется при помощи разного рода направляющих. Однако как же обрабатывать сложные фигуры?
Самые простые задачи, возможно, осуществить при использовании станков ЧПУ, но цена высока у производителей, и тут вы можете собрать сами себе станок как еще в просто народе называют самодельный ЧПУ станок. Но данный метод имеет свои минусы, потому как требуется сделать исходный шаблон, а также механические приспособления способны обрабатывать заготовки по определенному размеру. Самое главное, что подобные приспособления допускают большую погрешность. Выход из положения есть – станок с ЧПУ, который позволяет выполнять резку сложных фигур.
Данный аппарат имеет координатный инструмент для резки, управление которым происходит за счет компьютерной программы. Рабочий инструмент движется по заготовке с той траекторией, которая будет задана. Станок имеет безграничные возможности. Но есть у него немаловажный минус – большая себестоимость, что ограничивает его доступность. Остается найти оптимальное решение – сделать приспособление своими руками.
Принцип функционирования
Основа аппарата состоит из жесткой рамы. Обязательно необходимо иметь ровную поверхность, которая послужит основой. Это же является рабочим столом. Важный элемент – каретка, на которой установлен инструмент. В качестве такого приспособления можно взять ручной фрезер или дремель, то есть всевозможный инструмент, благодаря которому будет возможна обработка материала. Каретка двигается только по плоскости рамы.
Варианты оформления
Рамой бля будущего станка будет служить поверхность стола. Чтобы рабочий инструмент двигался в одном направлении, необходимо использовать две направляющие. Их нужно разместить параллельно одно к одной. Поперек монтируется мостовая конструкция, которая также должна быть сложна с двух направляющих.
Также можно использовать другую концепцию. Инструмент с кареткой устанавливается неподвижно, движение рабочей базы с заготовкой. Разница отсутствует. Только объем заготовки будет ограничен. В таком случае будет упрощена концепция электропитания, потому как беспокоиться о гибкости кабелей не потребуется. Решение можно выполнить следующим образом: стол может передвигаться по одной оси, а каретка с материалом для резки по другой.
Последний вариант оформления станка с ЧПУ – трехкоординатная система. Самостоятельная сборка займет больше времени. Для того чтобы инструмент был более функциональным и располагал тремя траекториями перемещения, на каретку монтируется дополнительный комплект направляющих. Какие возможности открывает такой принцип? Первоначально, есть возможность выполнять резку замкнутых фигур в самом центре режущего материала. Фреза будет размещена в начале разреза, поместиться на установленную глубину, выполнить перемещение по контуру внутри, а потом опять возвратиться в начальное положение. Такой станок позволяет делать обработку трехмерных фигур. Шаговые двигатели используются для движения каретки по направляющим. Самостоятельная сборка отрывает возможность выбора привода. Когда необходима скорость – подойдет ременный тип привода. Чтобы получить максимальную точность, лучше установить червячно-резьбовой.
Сердце станка – блок для управления с возможностью программирования. Его составляющие:
Модуль ввода, который располагает концепцию обработки материала. В качестве инструмента управления подойдет компьютер;
Процессор, благодаря которому происходит преобразование электронной фигуры заготовки в команды для рабочего инструмента;
Блок управления рабочими механизмами (головка для резки, двигатели).
Когда в ваших планах работа с габаритными заготовками, станок необходимо производить из металла. По вопросу управления – габариты аппарата не важны, также как и материал, с которого сделана станина. Если на станке будет выполняться обработка небольших форм, то устройство можно сделать малогабаритным, взяв за основу фанеру. Материал обладает достаточной жесткостью, что не даст возможности пружинить во время рабочего процесса, что крайне важно для точности обработки. Самое важное преимущество дерева, это его минимальный вес. Это говорит о том, что можно обойтись небольшим сервоприводом, который требует небольшое количество электроэнергии. Однако следует помнить, что направляющие в любом случае производятся из металла. Это обусловлено тем, что данный элемент поддается износу, а также он несет ответственность за точность работы инструмента.
Есть еще один вариант – станок ЧПУ с лазером. Дорогостоящая лазерная пушка способна резать материалы, но её непосредственное использование заключается в художественном выжигании.
Делаем выводы
Произведенный своими руками аппарат обязательно должен иметь качественные комплектующие, ведь это решит его точность выполнения обработки. После того, как электронные детали полностью подключены, следует заняться установкой программного обеспечения. Во время их выбора, нужно учитывать работоспособность, чтобы аппарат не имел ограничений в плане функционала.
Станок с числовым управлением сделать самому вполне возможно. Без определенных финансовых расходов обойтись не удастся, потому, как часть элементов для сборки в домашних условиях попросту не соорудить. Однако если сравнивать с заводской моделью, то в случае собственноручного исполнения экономия будет значительной. По завершению сборки каждый останется довольным. Потраченное время и финансы вполне себя окупят. Когда станок будет полностью готов, его необходимо проверить на наличие ошибок, которые можно сразу же устранить. Главное верить в свои возможности и успешное завершение сборки гарантированно!
Так же советуем прочитать:
Изготовления ЧПУ станка что нужно знать при сборки
ЧПУ станок по дереву своими руками за 1 неделю это реально
Самодельные станки — NordicWoodJournal
Некоторые люди просто не могут согласиться на станки, доступные на открытом рынке. Они думают, что эти машины недостаточно хороши. Значит, делают сами. Более-менее профессиональные машины, сделанные опытными и заинтересованными подрядчиками. Вот некоторые примеры.
Конечно, чтобы построить свою машину, вы должны обладать некоторыми навыками конструирования. Или, вы должны знать кого-то, у кого есть. Как Starks Flis AB, что мы писали о в феврале прошлого года, который хотел измельчитель с дистанционным управлением. Они позволили классическому конструктору лесозаготовительных машин Л. Л. Маскинеру построить машину в соответствии со спецификациями Старка.
Полный вперед! Дробилка оснащена двигателем Scania V8 мощностью 580 л.с. Форвардер — Valmet 860 2004 года выпуска. (В 2005 году он стал Komatsu)LL Maskiner — компания, которая построила харвестер «Spindeln» («Паук»), который позже стал SkogsJan, затем Caterpillar, а сегодня EcoLog.
Самодельные машины – с коммерческим назначением Как упоминалось ранее, я работал на выставке лесоводства Elmia, и мне очень хотелось, чтобы на выставке присутствовали разные машины. Я пригласил Starks Flis AB принять участие в выставке с их рубительной машиной с дистанционным управлением, но они не собирались продавать машину. Они просто хотели эффективную рубительную машину.
Но были и другие. Как T-Bear, о котором мы писали (среди прочих машин) в статье Odd Machines, который мог быть чем-то . В данном случае у изобретателя было четкое представление о выводе машины на рынок. Тем временем он использовал его в своей повседневной работе по заготовке леса. Однако T-Bear не удался, и был построен только один. Изобретатель T-Bear хотел выйти на рынок, но рынок не был заинтересован (?).
В той же статье упоминается немецкий инженер Юрген Хартиг и его электрический комбайн с маятниковой рукой. Этот проект до сих пор никогда не сходил с чертежной доски. Но г-н Хартиг построил свой собственный комбайн до этого. Первоначально он использовал себя, потому что SkogsJan не был готов выйти на новый рынок. Позже он продал концепт производителю машин, который построил серию из семи машин. Но оригинал у него до сих пор во дворе.
Наконец-то у нас появились настоящие самоделки. Тем, кому просто нужен станок и есть навыки мышления и сварки. И обычно куча металлолома для начала. Этот тип машин встречается чаще, чем кажется. Ты натыкаешься на них время от времени. Владельцы/строители, конечно, не хотят продавать машины, потому что они в основном незаконны. Они не были протестированы и не имеют сертификатов, таких как CE или аналогичные. Другими словами, они могут быть смертельными, и их нельзя показывать на публике или эксплуатировать незнакомцы.
Я ничего не могу с собой поделать, но этот тип машин я нахожу самым захватывающим. Они там, потому что у владельца было время и интерес к его строительству. Может быть, он или она даже нуждались в этом, но это, вероятно, не было важно.
Когда вы работаете в лесу, как я, вы их видите. Но у вас должны быть острые глаза. Здесь ниже тот, который переправлял дрова, которые я срубил прошлой зимой. «Настоящая» самодельная машина. На базе трактора Volvo BM 400.
Было бы интересно увидеть больше таких «настоящих» самодельных машин. Пожалуйста, дайте мне знать, если вы видели или видели какие-либо.
Фотографии: Per Jonsson
Per JonssonЯ начал свою первую собственную бензопилу в 1978 году. Выставки лесного хозяйства Elmia. Попутно я также получил образование лесничего. Я присоединился к команде NordicWoodJournal.com в качестве внештатного редактора в январе 2020 года.
Предыдущая статья
Топоры – Если бы они могли говорить…
18 июля 2022 г.
Следующая статья
Interforst 2022 – Куда катятся лесные выставки?
22 июля 2022
самодельных машин? | Главная Модель Форум машинистов двигателей
Лоренц
Участник
- #1
Я спрашивал себя, есть ли кто-нибудь, кто делает машины для хобби?
Поскольку у большинства людей на этом форуме есть металлообрабатывающие станки,
Есть ли хобби в изготовлении станков? или весовые машины?
Я увидел в гугле примеры самодельных гравировальных станков и самодельных моторизованных ножовок, вот я и подумал,
может есть люди, которые делают такие станки, как фрезерные станки или мини-токарные станки для удовольствия?
привет!
грабли60
Известный член
- #2
старых копий чертежей.

Это моя любимая ссылка для некоторых планов: Винтажные проекты .
Рик
Дэн Роу
Известный член
- #3
На фото размер парового молота Stuart рядом с прессом Minitool.
Привет Дэн
Твмастер
Известный член
- #4
Когда меня перевезут, я планирую построить электрическую ножовку.
Драйвер GWR
Старший член
- #5

Что касается увлечения изготовлением моделей станков, то есть ряд людей, которые этим занимаются или занимаются этим с впечатляющими результатами. Для начинающих (и продолжающих) посетите веб-сайт «Музей мастерства» для получения дополнительной информации.
Омнимилл
Известный член
- #6
Потрясающая работа!
Вик.
Майнер
Старший член
- #7
И PM Research продает серию наборов станков в масштабе 1:12, показанных на других фотографиях как часть настольной витрины PM Research в Cabin Fever.
Твмастер
Известный член
- #8
Вау.
Майнер
Старший член
- #9
Блогведьма
Ex Bogstandard
- #10
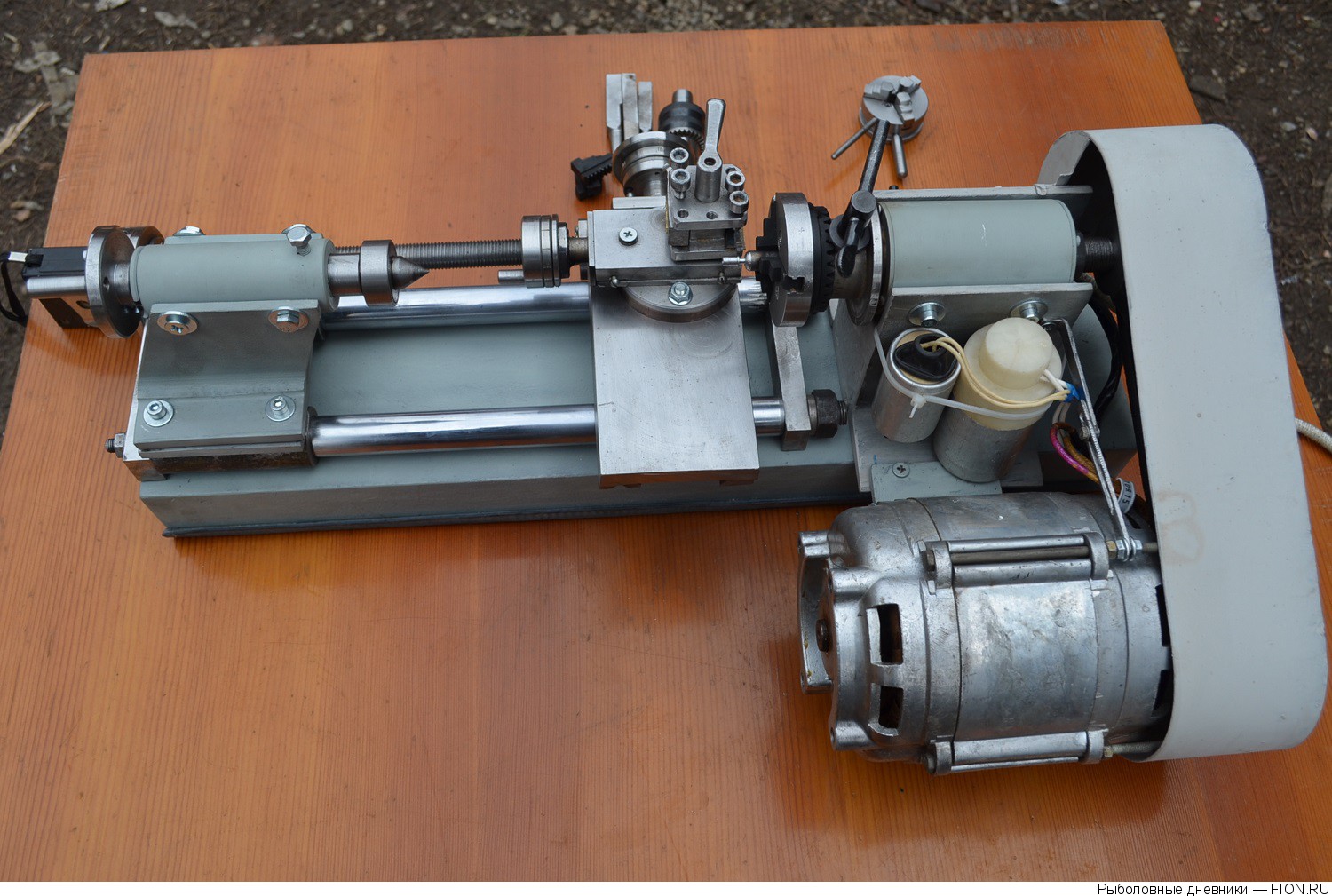
Когда я делал модели лодок, я сделал миниатюрный вертикальный настольный фрезерный станок и миниатюрную настольную пилу (диск диаметром 2 дюйма), в основном для резки тонких полосок шпона. Оба они теперь находятся в магазине друзей, где он использует их в изготовление кукольных домиков и их крошечной мебели. Они использовали в основном лист ПВХ для основного кузова и работали на двигателях постоянного тока 12 В.
Теперь у меня есть все, что нужно, чтобы сделать мою собственную алмазную притирочную пластину с водой для заточки практически любого инструмента, но особенно токарные инструменты.Для этого будет использоваться медленно работающий сетевой двигатель (250 об/мин), взятый из перистальтического насоса.
Обычно я использую все, что есть в магазине, для изготовления подобных инструментов, а основной корпус будет сделан из имеющегося у меня акрилового листа толщиной 12 мм с металлической облицовкой в местах износа.
Блоги
kcmillin
Победитель проекта месяца!!!
- #11
Вот парочка, которую я использую постоянно.
На основе ручных тисков, которые я видел в каталоге. Я использовал орех для ручки. Я тоже сделала четыре штуки и раздала в подарок. Не могу найти их в строительном магазине.
Вот 3-дюймовые фрезерные тиски, которые я сделал из большого куска стали. Это очень удобно, когда нужны маленькие тиски.
кел
Новый_Парень
Известный член
- #12
я буду держать рот на замке, чтобы вы, ребята, не видели всей серьезности моего состояния :hDe:
Оловянный сокол
Известный член
- №13
Лоренц:
Да, производство миниатюрных инструментов, безусловно, является отраслью или подразделением модельной инженерии или инженерии в миниатюре. Как уже упоминалось, есть несколько поставщиков, которые предлагают комплекты мини-станков. Я не припоминаю много доступных наборов планов, я думаю, что большинство людей копируют машины, которые у них есть. Как указано на нашем баннере, этот сайт посвящен моделям двигателей из сортового проката. Это не означает, что вы не можете публиковать сборки моделей машин. Мы будем рады видеть такие сообщения, и они будут поощряться. Вы можете не получить много помощи просто потому, что это не область знаний форума.
Олово.
ДейвсВимшерст
ДейвсВимшерст
- №14
Ленточная пила для резки металла и дерева, колеса 17,5 дюймов, скорость от 115 до 3350 футов в минуту с использованием смены ремня и редуктора:
ленточная шлифовальная машина:
В этой машине используются ленты размером 1 x 42 дюйма.
Исследовательский токарный и сверлильный станок PM
Дэйв
кункв
Известный член
- №15
Я еще не построил ни одного готового станка, но я работаю над преобразованием токарного станка Taig в ЧПУ.
Спасибо за пост. Самодельные машины мне всегда интересны.
С уважением,
Чак
E Крис
Участник
- №16
Кажется, некоторые из нас любят делать маленькие станки.
Одних больше интересует форма, других функция. Английский автор Л.К. Мейсон написал прекрасную книгу под названием «Создание маленького станка». Эта книга будет очень полезна любому, кто собирается построить небольшой токарный станок. Билл Хаксхолд — человек, который в высшей степени сочетал форму и функцию. Модель токарного станка Хардинга мистера Хаксхолда, по всей вероятности, так же хороша, как и прототип.
Недавно я сделал небольшой поворотный инструмент и точильный станок. Он может иметь горизонтальный (показан) или вертикальный шпиндель. Как видите, я определенно нахожусь в лагере функции, а не формы.
Крис
Новый_Парень
Известный член
- # 17
вау Крис это просто потрясающе!!
изогнутый
Известный член
- # 18
Что касается механических машин, я сделал 6-дюймовую дисковую шлифовальную машину, используя двигатель заводского вытяжного вентилятора. В качестве подложки используется диск из МДФ. но сейчас я делаю это нечасто
Я также сделал маленькую циркулярную пилу, используя двигатель от старого сверлильного станка. Лезвие было 2-дюймовым лезвием Minicraft, которое лежало в ящике стола не менее 10 лет!
Когда я думаю об этом, я сделай несколько фото.
Крис, это хорошая работа, не хочешь рассказать об этом немного больше? я не совсем понимаю, как это работает.
1 рука
Известный член
- # 19
Матовый
E Крис
Участник
- #20
Спасибо за добрые замечания. Я считаю, что они называют этот тип гриндером, и это действительно так. Колонна и, конечно же, головка/мотор могут свободно раскачиваться из стороны в сторону, подниматься и опускаться. В нижней части колонны находится шарикоподшипник, который действует как упорный подшипник, а в верхней части находится тонкий (40 т/д) подъемный винт с ходом около полудюйма. 40 tpi и большой градуированный маховик обеспечивают контроль высоты с точностью до тысячной доли. Грубый винт сзади предназначен для грубой регулировки высоты и заблокирован знающими людьми на боковой стороне руки. Как я упоминал в предыдущем посте, узел горизонтального шпинделя можно заменить вертикальным шпинделем для использования чашечных шлифовальных кругов. Вертикальный шпиндель будет выполнять двойную функцию, когда я закончу кофемолку Quorn. Мой сын называет это измельчителем жестяных банок, потому что я использовал банку, чтобы сделать пылезащитный экран для колонки. Опорная плита и, конечно же, основание колонны — это ненужные части компьютерной ленты мейнфрейма.