Чпу фрейзер – .
Домашний ЧПУ-фрезер как альтернатива 3D принтеру, часть первая — выбор станка / Habr
Последнее время на хабре все чаще появляются топики, посвященные 3D-печати вообще и домашним 3D-принтерам в частности. И почти в каждом в комментариях вспыхивает холивар между романтиками, в жизни не видевшими 3D отпечатков, и практиками, единожды потрогавшими и разочаровавшимися. При этом вторые почему-то не приводят адекватных альтернативных технологий, комментарии носят либо чисто критический характер, либо предлагают заведомо более дорогие альтернативы. Тем не менее, достойная альтернатива есть — домашний фрезерный станок с ЧПУ.Звучит удивительно, да? Как-то само слово станок в народе ассоциируется с производством, с отдельными помещениями и специально обученным персоналом. В действительности, существует большой класс ЧПУ-станков, рассчитанных на настольное использование в офисе и на малых производствах, а при желании — и дома. При этом цена маленьких ЧПУ-фрезеров приближается (чтобы не сказать равна) к реальной цене 3D-принтеров.
Жизнь сложилась так, что последний год с гаком я занимаюсь изготовлением литьевых форм для полиуретановых изделий на ЧПУ-фрезере. Поскольку до этого 10 лет оттрубил в IT ритейле, а образование не имеет никакого отношения ни к инжинирингу, ни к ЧПУ, осваивать технологии пришлось с нуля. За прошедший год я подрос с должности оператора-фрезеровщика до инженера-конструктора, а затем и до замдиректора по технологиям, моими стараниями ЧПУ-парк предприятия вырос с одинокого старенького роланда до 5 разнокалиберных станков. В связи с чем еще свеж и актуален опыт выбора, покупки, пусконаладки, тюнинга, эксплуатации и ремонта различных ЧПУ-станков.
И вот — решил поделиться опытом с сообществом. Я осознаю сам, и прошу принимать во внимание читателей, что я — самоучка без базового инженерного образования, все нижеизложенное основано исключительно на личном опыте.
После долгих мук выбора, писать статью-противопоставление или статью-обзор технологии победил третий вариант: написать цикл статей, описывающий слегка абстрагированный опыт ЧПУшника — от выбора станка, пусконаладки и инструментов, через подбор материалов, ПО и режимов работы, до тюнинга и доводки.
Под катом первая статья цикла — краткое описание подсистем ЧПУ-фрезеров, с комментариями и рекомендациями по выбору.
Что купить и как выбрать
В первую очередь определяемся с задачами.
Поскольку мы смотрим на альтернативы 3D принтерам для домашнего/хоббийного использования, основными рабочим материалами у нас будут пластики, дерево, МДФ, ДСП, фанера, текстолит и немножко цветмета. Размеры — не менее домашние 20*30 см — размер листа А4.
Шпиндель
Шпиндель — рабочий инструмент станка, вращающий фрезу. Мощность шпинделя является производной от желаемой скорости съема материала: у меня есть вполне неплохой опыт фрезеровки алюминия 60Вт шпинделем, но с убого маленькими подачами и заглублением. В большинство китайских станков устанавливаются шпиндели 600-800 Вт, чего вполне достаточно для чистого съема пластика/дерева глубиной 1 мм со скоростью 2 метра в минуту.
Отдельно предостерегу от использования шпинделей Kress FHE/FE серии: по сравнению с китайцами они в разы более шумные и менее точные. Если продавец предлагает установку такого шпинделя, лучше закажите сами нормальный шпиндель на алиэкспрессе, а еще лучше — найдите другого продавца.
Рама
Направляющие
Для озвученных размеров подойдет станок на круглых направляющих 16-21 мм.
вообще, эмпирическое правило для заявленных целей «длина-направляющие»:
15-40 см — 16 мм круглые
40-90 см — 22 мм круглые с основанием
Механика
Поскольку мы заявили цветмет в целях использования, передача усилия с моторов на ось должна быть достаточно жесткой. Потому — долой ремни, да здравствуют ШВП и винты. ШВП — это шарико-винтовая передача, фактически — тот же винт, только канавки резьбы полированы и гайка представляет собой шариковый подшипник. ШВП имеет значительно более плавный ход, выше точность и надежность. Так что винт, пожалуй, допустим только на оси Z, которая по определению менее подвижная, чем остальные.
Передача усилия с моторов на винты для наших задач не критична — достаточную жесткость обеспечивает и ременная передача, и редуктор и муфты. Опять же главное — чтобы между мотором и винтом было что-то, компенсирующее биение оси и резкие усилия в начале движения, а то китайцы в целях экономии могут и напрямую шаговик прикрутить к винту, что отрицательно скажется на продолжительности жизни моторчика.
Моторы
В хоббийном сегменте однозначно рулят шаговые двигатели, они же шаговики. Причем для заявленных целей вполне достаточно фактически любого современного движка, начиная от 42/48 с усилием 5,5 кгсм. Из дополнительных плюшек, предлагаемых станкостроителями можно отметить рукоятки на оси, энкодеры, и прочее — в наших задачах это некритично.
Электроника
Стол
Стол должен быть. Поскольку во многом точность детали определяется жесткостью крепления, стол должен быть жестким. А дальше — пошли вариации. Китайцы в свои станки любят ставить столы из конструкционного профиля с Т-образными пазами — достаточно удобно и универсально, но не очень жестко. Гораздо лучше — плита с сеткой отверстий с резьбой. Наиболее универсально, но дорого и замороченно в эксплуатации — вакуумный стол.
Плюшки и дополнения
Важным подспорьем являются концевые датчики на всех осях и датчик нуля оси Z.
Специфические дополнения — дополнительная (вращающаяся) ось, DSP контроллер, датчик положения, щуп, энкодеры, специальные зажимы и т.д., но все это, пожалуй, уже выходит за рамки статьи для начинающих.
Интерфейс и ПО
Поскольку мы говорим о фрезерах низшей ценовой категории на шаговых двигателях без энкодеров, штатный интерфейс будет в лучшем случае слегка кастомизированным PCI-LPT контроллером с опторазвязкой, в худшем — просто кабелем к LPT порту компьютера. По-моему, примерно один черт, по крайней мере я не заметил разницы в работе.
Программное обеспечение разнообразно, но функционально сводится либо к простому интерпретатору G-code в сигналы драйверов шаговых двигателей, либо к более продвинутому эмулятору стойки управления станка. В любом случае, если штатная программа не удовлетворяет, можно немножко помучиться и состыковать станок с LinuxCNC, который по функционалу и удобству не уступает продвинутым фирменным решениям.
Пожалуй, на этом статью можно и завершить, будут вопросы/пожелания/дополнения — велкам в комментарии и ЛС.
В следующей части — обзор режущего инструмента, крепеж, аспирация, СОЖ в домашних условиях.
Обзор бюджетного ЧПУ фрезера CNC 3018
ЧПУ станок CNC 3018 с Китая
Решил я приобщиться к теме ЧПУ станочков, и прикупил себе CNC 3018 как для общего развития, так и для нарезания на нем всякого добра из фанерок и текстолита. На форуме уже проскакивали обзоры по теме CNC, я бы хотел поделиться своими ощущениями от покупки. Я не буду подробно описывать сборку механической части ( в комплекте идет подробная инструкция, да и просто по фотографии станка на странице товара собрать что-то неправильно очень тяжело ) а постараюсь остановиться именно на вещах, которые вызвали затруднения или были не очевидны.
Нюансы, вылезшие еще на этапе сборки.
Первое — уголки, выполненные из цинкового сплава, нуждаются в небольшой шлифовке поверхностей, соприкасающихся с профилем. Благо, что облой удаляется надфилем буквально за пару секунд. Уголков, кстати, в коробке на 2 больше, чем необходимо для сборки.
Второе, и самое интересное – одевание патрона цанги на вал двигателя. Первый двигатель с патроном я испортил – нагрел феном патрон, остудил двигатель в морозилке, совместил, пара легких ударов через деревяшку, вал идет крайне туго, пара ударов посильнее… В общем патрон сел на 8 мм и все, сдвинуть его теперь невозможно ни в одном, ни в другом направлении.
Двигатель крутится, ощутимых рукой люфтов нет, но звук из подшипников стал громче. Допуски на диаметр вала и посадочного отверстия в патроне гуляют, и у кого то он просто одевается «на холодную», а кто-то не смог нормально одеть и «на горячую». Вывод прост – для уверенности нужно греть патрон градусов до 300 и одевать очень быстро, пока патрон не прогрел вал и не расширил его, и надеяться что вы не попали на крайний случай, когда вал с большим допуском «в плюс», а отверстие в патроне «в минус». После я поменял двигатель с патроном, нагрев последний в духовке. Сел «впритирочку».
Провода, идущие к двигателю, я позже заменил на силиконовые с чуть большим сечением, усадив скрутку из них в термоусадку. Никаких систем для организации кабельного хозяйства, кроме десятка нейлоновых стяжек, в комплекте нет. Пока будем довольствоваться колхозом. Сразу выведем щупы Z и организуем им парковку. При гравировке печатных плат они пригодятся для поиска нуля по Z и составления карты высот в Candle.
Третье. Мне не повезло, и стол пришел кривой, я бы даже сказал дугообразный. Я даже не стал пытаться его ставить (без шаманства с подкладываем всякого при креплении к столу суппортов с подшипниками и гайкой ходового винта он бы вообще не мог ходить по валам), а сразу написал продавцу и на следующий день получил трек код посылки, в которой приехал новый стол, к счастью, прямой.
Устанавливаем необходимый софт. Так бы я и сидел со старой версией прошивки grbl 0.9j, привязанный к версии Candle не выше 1.0.11, но случилась еще одна неприятность. После «тыканья» USB-осциллографом на контакты шпинделя в целях посмотреть там ШИМ (DS205 только пришел, и станок стоял на столе, я не удержался, и предвосхищая нападки сразу укажу – он был подключен к ноутбуку, работающему от батареи) плата контроллера перестала подавать признаки жизни и на ней постоянно горели светодиоды Rx и Tx. Было решено перекинуть микросхему контроллера Atmega328P, но даже со снятой микросхемой (аккуратно выкушенной, ручка фена была еще в пути на момент аварии) светодиоды продолжали постоянно гореть, что указывало на гибель микросхемы Ch440 (преобразователь USB-SERIAL TTL), и она была заменена. Контроллер Atmega328P был поставлен чистый, все было соединено по стандартной схеме для заливки bootloader-а в чип и последующей загрузки самой прошивки grbl 1.1f.
Но чуда не произошло, avrdude говорил о неправильной сигнатуре контроллера, и даже после ее подмены отказывался нормально заливать bootloader. Танцы вокруг прошивки продолжались еще долго, и я перейду сразу к тому что сработало — для исключения влияния самой платы woodpecker нужные ноги Atmega328P были приподняты над ней и кинуты проводки напрямую к Arduino NANO, используемой как ISP.
И о чудо, bootloader успешно залился, я подключил USB к самой плате woodpecker и через XLoader залил новую прошивку grbl 1.1f.20170801. После этого ноги микросхемы были возвращены на законное место. Эпопея с поломкой и починкой заняла три вечера, и подняла мой уровень общения с современными микроконтроллерами. Через командную строку в Candle или монитор порта в Arduino IDE необходимо настроить параметры прошивки (указаны значения, установленные мною, которые вполне могут не подойти другим):
$100 = 800,000 Число шагов на мм. по оси X, шаг / мм. Тут, как и в двух последующих пунктах, ничего настраивать не пришлось.
$101 = 800,000 Число шагов на мм. по оси Y, шаг / мм.
$102 = 800,000 Число шагов на мм. по оси Z, шаг / мм.
$110 = 600,000 Максимальная скорость перемещений по оси X мм / мин. Я хотел поставить скорости по X и Y поменьше, но на более низких скоростях звук был крайне неприятным, а вот 600 звучало не слишком громко и напрягающее.
$111 = 600,000 Максимальная скорость перемещений по оси Y мм / мин
$112 = 150,000 Максимальная скорость перемещений по оси Z мм / мин. Тут я решил что спешить мне некуда, а испорченная заготовка / сломанная фреза удовольствия доставят минимум.
$121 = 30,000 Ускорение по оси Y (чем больше значение тем быстрее разгон) мм / сек ^ 2
$122 = 30,000 Ускорение по оси Z (чем больше значение тем быстрее разгон) мм / сек ^ 2
Настраиваем ток шаговых двигателей. Приходят они настроенными как попало. У нас установлены шаговики 17HS1352-P4130 с номинальным током фазы 1.33 А. Драйвер установлен A4988, с предельным током 2 А и токозадающими резисторами 0.1 Ом.
Настраивать будем используя следующую формулу:
Imax = Vref /8*Rs
Vref удобнее всего измерять прямо на движке подстроечного резистора относительно земли (она выведена на весь нижний ряд гребенки 2.54 мм.), можно даже совместить, подцепив крокодил на отвертку (учитывайте, что при нажатии на подстроечник показания немного уплывут).
Выставив 0.64 В я получил ограничение рабочего тока в 0.8 А. В требования для шаговика мы укладываемся, а запас позволяет снизить нагрев драйверов и самих двигателей (а он весьма ощутим если они стоят на удержании).
В комплекте к станку нет никакого намека на концевые выключатели. Я решил сразу подключить имеющиеся в запасе концевики и настроить работу прошивки с ними. Мы можем работать с концевиками двумя способами – с нормально разомкнутыми, и нормально замкнутыми. Дабы исключить ложные срабатывания, был выбран второй вариант, к тому же он сокращает расходы провода. При нем концевики подключаются последовательными парами для каждой оси (в варианте с нормально разомкнутыми – параллельными).
На гребенке платы выведены контакты для подсоединения концевиков, тянуть лишние провода не стоит, так как контакты запараллелены для каждой оси. Я использовал экранированный провод, немного алюминиевого профиля, крепежа и нейлоновых стяжек, а так же творческий запал. К каретке оси Z весь профиль для крепления концевиков и упоры крепились мелкими саморезами с предварительным засверливанием и проклейкой отверстия.
После сборки электромеханической части, приступаем к настройке прошивки.
$5 = 1 Инвертирование входов от конечных датчиков (концевики), BOOL. Для нормально разомкнутых выставляем 0.
$21 = 1 Включить ограничение по концевым датчикам, BOOL.
$22 = 1 Автопозиционирование по концевикам, поиск точки Home, BOOL. Включил, чтобы было удобно, нажал кнопку в Candle, и станок сам встал домой (в ноль).
$23 = 3 Маска инвертирования направления движения к точке Home (маска: 00000011). По умолчанию станок уползал в конец по осям X и Y, пришлось по ним инвертировать направление движения. Маска соответствует маске для $3 = XX – инвертированию направления осей.
$24 = 30,000 Скорость движения у концевиков, мм / мин. Это скорость движения после того, как станок наехал на концевик в поисках home в первый раз и, отскочив, начал медленно наезжать вновь. Она намного ниже для более точной фиксации момента срабатывания концевика.
$25 = 300,000 Скорость движения к точке Home, мм / мин. Скорость, с которой начнется движение к концевикам независимо от положения станка. Если она выше максимальной скорости по какой-либо из осей, то ограничение будет выставлено по нижнему порогу.
$26 = 250 Задержка срабатывания концевиков (антидребезг) мс. Использую такую дешевую механику как у меня, ставить ниже наверное не стоит.
$27 = 2,000 Расстояние «отскока» от концевиков, мм. На это расстояние отскочит станок по всем осям после того как встанет в точку home.
Станина станка сильно вибрирует, вокруг летит пыль, а плата такая незащищенная, и к тому же горячая — строим «скворечник» для нашего «дятла». Корпус от распределительной коробки освобождаем от внутренного богатства, рассверливаем отверстия под крепеж платы и под крепеж самого корпуса к раме. К раме крепим его через антивибрационные стойки от старого CD-ROMа. В верхней крышке вырезаем окна для кабельного хозяйства и устанавливаем 80 мм. вентилятор. Запитываем его от отдельного DC-DC, чтобы можно было выставить обороты.
Для питания самого DC-DC 12 В берем с разъема на плате, расположенного над входным электролитом, никак не подписанного, но скорее всего для вентилятора и служащего.
На этом основные трудности заканчиваются, и можно опробовать станок в деле.
Нужен был аккуратный чистый рез добора из МДФ, при подаче в 50 и ручном управлении фрезой-кукурузой 2 мм с заглублением 1 мм за проход отрезаем. Долго, но рез получился что надо, немного проходимся наждачкой по фаскам.
Задачка посложнее – гравировка печатных плат. Берем старый кусок советского текстолита (кстати, постарше меня будет, по наследству достался) и делаем дорожки. Результат рядом с резистором 1206.
Теперь изготовим платку для симистора с опторазвязкой, для усложнения ставим заготовку по центру стола, где люфты на длинных валах оси X максимальны:
Результат так себе. Я грешил на люфт, но проблема была не только в нем. На первом тесте я использовал только штатные зажимы для крепления заготовки к столу, а в этот раз использовал толстый двухсторонний скотч. Он «играет», и поэтому с первого раза рез получился не везде, пришлось делать заглубление больше, а так как гравер имеет треугольную форму, то он подрезал край дорожки, и они стали уже и качество самого реза снизилось. Так же выяснилось, что китайские гравера обламываются даже при самой маленькой подаче и заглублении всего в 50 мкм. Но обламываются по-разному, и один потом может делать чистый аккуратный рез, а другой будет задирать края. Третий обломившийся гравер на следующей печатной плате снимал стружку длиной во всю дорожку, как результат рез получался чище. Видимо, в пользу советского текстолита сыграла так же и общая его жесткость, и гораздо более толстый слой меди. С креплением заготовок печатных плат придется поломать голову. Во первых, оно должно быть по всей нижней поверхности, чтобы не было «пузырей», которые бы играли под фрезой. Во вторых, оно должно быть надежным, при отрезании заготовки ее легко может вывернуть, на фото ниже на плате перерезана дорожка в правом верхнем углу фрезой. И в третьих, оно должно быть устойчиво к воде, так как во время работы заготовку стоит помочить и избавиться тем самым от текстолитовой пыли. И если для мелких плат комплектное крепление годится, то уже платы размером больше 70×70 мм они крепят с горбинкой. Вот фото работы станка после учета недостатков крепления.
Плюсы CNC 3018:
+ Вы получаете возможность начального знакомства с ЧПУ с минимальными затратами времени, но при наличии последнего в некотором количестве, вы так же бонусом получаете возможность по совершенствованию самого станка, а параллельно и своих навыков.
+ Станок из коробки способен на работу после минимальной настройки.
Минусы:
— Качество запчастей может хромать. Нет никакой гарантии, что после получения станка вам не придется ждать еще, чтобы наконец-то получить какие-то запчасти взамен бракованным.
— Пластиковая каретка оси Z. Мне кажется, что станок все же должен быть более прочным.
— Огромный вылет по оси X приводит к тому, что когда каретка находится на середине этой оси, она имеет существенный люфт, так как вал немного прогибается. Это в свою очередь может приводить к резонансу всей конструкции на высоких оборотах шпинделя (порядка 10 000 об/мин). Заменив шпиндель на более оборотистый, можно уйти от резонанса, работая на оборотах, выше критических, да и для фрезеровки ПП он подойдет наверное лучше. Но гораздо правильнее – поменять слишком хлипкие валы по X с текущих 10 мм на минимальные 16 мм. Однако, это приведет к необходимости полной замены каретки оси Z. В будущем, я, наверное, так и поступлю, ту часть каретки что с подшипниками, гайкой и креплением шпинделя оставлю, а заднюю половину, наверное, придется сделать из фанеры/ламината на самом станке.
— Для каждого вида работ нужно искать подходящую оснастку. Гравера из комплекта оставляют желать лучшего. Так же придется освоить приличное количество программного обеспечения для раскрытия потенциала станка.
Выводы: если у вас есть время и желание возиться и дорабатывать станок до ума, но вы не готовы к самостоятельной закупке и сборке с нуля, то вариант с покупкой такого конструктора можно считать оправданным. Для тех кто не знаком с ЧПУ, но очень хочет познакомиться, наверное, будет намного проще начать именно с такого конструктора, чтобы понять, нужно оно вам или нет. Если же у вас есть желание работать именно на результат, то целесообразнее станок собирать по частям, чем дорабатывать этот, так как цена доработок сопоставима со стоимостью всего станка.
Где купить ЧПУ фрезер CNC 3018
3018 3 Axis Mini
Стоимость: 289.9 $ |
Лазерные модификации этого станка
CNC 3018 500мВт
Купить: BangGood CNC 3018 2500мВт
Купить: BangGood CNC 3018 5500мВт
Купить: BangGood
автор: Am0k
Источник
hobby-cnc.ru
Домашний ЧПУ-фрезер как альтернатива 3D принтеру, часть вторая / Habr
На днях устыдили меня, мол ругаюсь на дилетантов, а сам ничего хорошего не пишу, а обещал ажно «цикл статей». Пришлось достать старый черновик и доработать. Для забывших — первая часть про выбор станка тут.Предположим, что Вы определились с моделью фрезера, провели первичные переговоры с поставщиком и начали морально готовиться к покупке. Что еще понадобится для начала работы?
Хотя многие поставщики вкладывают в комплект «стартер кит», для комфортного домашнего использования он будет явно недостаточен. Так что сразу начинаем искать/покупать/делать следующее:
— Режущий инструмент — фрезы/граверы и боры
— Дополнительные цанги к шпинделю
— Крепеж для стола
— Систему изоляции и/или удаления стружки
И да, сразу оговорюсь: данная статья касается домашних фрезеров со шпинделями типа Kress или китайчонками с цангой Er11, поэтому во-первых предположим, что хвостовик фрезы у нас цилиндрический до 6 мм (у Кресса есть 8, но нормальной его работу с 8кой не назовешь — слабенький он таки), во-вторых, механический инструмент смысла не имеет — мощи не хватит, а в третьих, сверла-развертки-метчики-флайкаттеры недоступны, поскольку минимальная скорость — 6000 оборотов.
Режущий инструмент
Станок у нас фрезерный, так что о фрезах в первую очередь. Фрезы подразделяются по:
1. Профилю режущей кромки
1.1. Прямые (end mill) — фреза с рабочей областью цилиндрической формы, дающая в идеале паз с идеально прямоугольным дном
1.2. Круглые (ball mill) — фреза с рабочей областью, оканчивающейся радиусом, дающая в идеале паз с радиусными стенками
1.3. Bull nose mill — прямая фреза со скругленным краем, дающая паз с прямым дном, но радиусным переходом между дном и стенкой.
1.4. Конические (cone mill) — фреза с конической рабочей областью, заканчивающейся радиусом или прямой площадкой
1.5. Фасонные (profile mill) — фрезы с определенным профилем, в случае с ЧПУ могут иметь смысл либо для ускорения работы, либо для создания поднутрений.
1.6. Пазовые (slot cutter) — фрезы для создания пазов с поднутрениями типа Т-пазов, ластохвостов, О-пазов и пр.
2. Способу отведения стружки
1.1. Спиральные с удалением стружки вверх — работают на большинстве материалов.
1.2. Прямые, они же half-pipe mill, они же граверы в русскоязыной литературе — без удаления стружки, подходит для слоистых материалов типа фанеры, гетинакса и пр, либо для раскроя листовых пластиков, когда спиральная фреза может поднять матерал над столом
1.3. Спиральные с удалением стружки вниз — для ламинатов, если важно обеспечить максимально ровный рез ламинирующего покрытия
1.4. Спиральные компрессионные — фрезы со переменной спиралью, нижняя часть отводит стружку вверх, верхняя — вниз, для двухсторонних ламинатов, чаще всего — для раскроя алюкобонда/дибонда.
3. Количеству режущих кромок
Для работы с пластиком/деревом обычно хватает одно-двухперой фрезы во всем диапазоне размеров, с цветметом 4-6 мм уже может понадобиться 3-4перая.
4. Отношению рабочей части к хвостовику
4.1. Равномерные — одинаковая рабочая часть и хвостовик.
4.2. Обниженные — хвостовик шире рабочей части. Актуально для мелких фрез.
4.3. Расширенные — часто для фасонных фрез, обычные такие в продаже не встречал, но сам делал, хвостовик уже рабочей части.
5. Материалу, углу заточки, углу спирали, покрытию и т.д.
Тут перечислять, пожалуй, бесполезно — технологий великое множество. Стоит только отметить, что производитель обычно пишет рекомендованный материал и качество обработки (черновое/чистовое), если вы закупаетесь на али, где продавец побрезговал давать рекомендации или рекомендации явно фейковые («суперчистовая обработка титан/алмаз/колбаса/фанера»), попробуйте найти аналогичную внешне фрезу (спиральная, один заход, желтенькая) у именитого производителя в каталоге и ориентируйтесь на эти данные.
Отдельно стоит выделить бор-фрезы — фрезы с большим количеством очень маленьких режущих элементов и относительно мощной сердцевиной. Такие фрезы предназначены для доводки или поверхностной обработки материалов типа шлифовки, снятия тонкого слоя, гравировки твердых материалов и т.д.
Теоретически, со станком можно использовать сверла, но не забывайте учитывать обороты. Все-таки сверла обычно рассчитаны на дрель, где обороты редко превышают 800 об/мин, а на обсуждаемых шпинделях 6000 минимум. Впрочем, для мелких сверел это будет скорее плюсом, но если речь заходит о 3 и более мм, во-первых постарайтесь приобретать сверла с покрытием, а во-вторых, стройте траекторию для сверления таким образом, чтобы сверло не успевало перегреться.
Цанги и переходники
Поскольку поставщик у нас в лучшем случае российский перепродавец, а в худшем — китаец, рассчитывать стоит на минимизацию комплекта. А боль-мень серьезная работа со станком подразумевает наличие некоторого количества фрез, скорее всего с разными хвостовиками. Теоретически, в продаже существуют переходники — дополнительные цанги, позволяющие вставить фрезу с хвостовиком 3 мм в цангу 6 мм, но стоит помнить что это во-первых снизит жесткость, а во-вторых снизит точность установки фрезы.
Конечно, набор цанг — вторичен от используемых фрез, если Вы уже определились с набором фрез, то можно не мудрствовать и набрать цанги под свой набор. Тем не менее, цанги обычно менее доступны, чем фрезы и можно оказаться в ситуации, когда фреза есть, а цангу под нее ждать с Китая 3 недели, поэтому рекомендую взять как минимум 3 штуки: 6 мм (максимальная), 4 мм (чаще всего под нее идут мелкие фрезы и конические граверы) и 3 мм (ровные чистовые фрезы).
Стандарт Er11 подразумевает полный диапазон от 0,5 мм по 7 мм с шагом 0,5, т.е. цанги идут 0,5-1, 1-1,5, 2-2,5 мм и так далее.
Крессовский шпиндель имеет проприеритарную цангу, но благодаря распространенности самого шпинделя и клонов/подделок, достать цанги не проблема. В наличии по магазинам обычно есть цанги 3,4,5,6 и 8 мм + 3.175 мм «американского стандарта», в котором у нас встречаются борфрезы и граверы. При этом сама цанга цетырехчастная, т.е. диапазон зажатия вряд ли сильно больше пары десяток, так что зажать фрезу с хвоствоиком 3.5 мм будет просто нечем. Впрочем, это вряд ли будет проблемой в домашнем применении.
Чуть не забыл: цанги обычно продаются отдельно от гаек. В принципе, нет никакой проблемы в перекидывании цанг в одной гайке, но мне лень, да и есть мелкая, но вероятность что при перекидывании занесешь в резьбу какой-нибудь мусор, а это опасно для резьбы.
Крепеж для стола
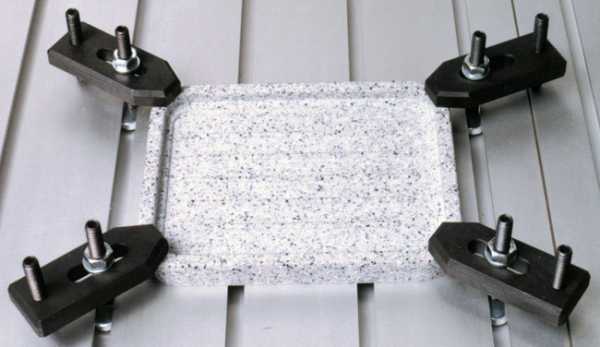
Большинство домашних роутеров оборудованы либо столом с Т-пазами, либо столами с сеткой резьбовых отверстий. И в том и в другом случае наиболее распространенный крепеж выглядит как стальной или алюминиевый прижим с одним резьбовым и вторым гладким отверстием. В Т-паз вставляется Т-болт, который проходит через отверстие прижима и фиксируется гайкой, второй болт отжимает прижим от стола. В комплекте со станком обычно идут 4 прижима, которые при интенсивной эксплуатации довольно быстро выходят из строя: срезаются резьбы на винтах и прижимах. Иногда китайцы вместо Т-болта кладут в комплект обычные болты и Т-гайки, рекомендую сразу озаботиться заменой на Т-болты.
Вместо задних (упорных) винтов можно приспособить куски материала или специальные ступенчатые клинья, но в случае работы со скользким пластиком это может сослужить дурную службу: крепеж будет «отползать» от фиксируемого материала.
Альтернативой прижимам могут служить станочные тиски — специальные тиски с минимизированной высотой и адаптированной для установке на столе рукояткой (или вообще под ключ). Плюс — мЕньшая морока при установке материала, повторяемость, относительная точность. Если Вы работаете с похожими небольшими заготовками, можно один раз в жизни выставить тисы, записать их координаты и в дальнейшем отталкиваться от них. Минусы — большая часть готовых тисков съедает 20-30 мм высоты минимум, а обсуждаемые станки редко имеют более 70 мм под порталом, ну и с большими размерами тисы обойдутся неимоверно дорого.
Еще один вариант — приклеивание заготовки к столу. Как ни странно, силы удержания на хорошем двустороннем скотче хватает даже на щадящую гравировку цветмета, не говоря уже о пластиках. В не к ночи упомянутом Roland даже в инструкции было что-то про скотч написано. Минусы очевидны: переменная надежность, ну и главное — отдирать уже готовое изделие, а потом чистить его от скотча.
Ну и напоследок — экзотика для домашних станков, вакуумный прижим. В принципе, не такая уж сложная штука, но требует дополнительного вакуумного насоса и таки сжирает 10 мм высоты минимум.
Система изоляции и удаления стружки
Одна из наиболее частых проблем использования роутера дома — шум и пыль. И если с шумом еще можно смириться, то пыль выбешивает конкретно. А в случае обработки камня/гетинакса/стекла/композитов — пыль еще и вредна.
Возможны 2 варианта борьбы: активная аспирация пылесосом со щеткой, смонтированной на шпинделе, и создание «кабинета» для станка.
Щетка вроде хороша, но при многочасовых траекториях рев пылесоса создает неповторимую атмосферу в доме. Ну и если идет глубокая выборка, ворс щетки постоянно изгибается и довольно быстро портится. Поэтому мы оставили систему аспирации только на самом большом фрезере, а мелкие убрали в кабинеты из прозрачного поликарбоната и ламината. Не так компактно, конечно, зато кабинет гасит и немножко звука, и пыль.
Мой личный набор «молодого бойца»
И напоследок — маленький бонус. Мой личный набор «молодого бойца», который я покупаю/делаю для каждого нового фрезера (основная работа — 3D фрезерование форм по ПП, ПОМ, ПЭТ, композиты):
Фрезы:
- 6 мм однозаходная прямая длинная — кромка 40 мм, общая длина 75, китайка.
- 6 мм шариковая хорошая (Widia/Makestag/SGS)
- 4 мм однозаходная прямая длинная китайка
- 3 мм двузаходная прямая длинная хорошая
- 3 мм двузаходная шариковая длинная хорошая
- 1,5 мм с удлиненной шейкой прямая хорошая
- 1,5 мм с обычной шейкой шариковая хорошая
- 0,8 мм с обычной шейкой шариковая, либо коническая с круглой пяткой 0,8 мм.
Цанги: 3, 4, 6 мм, все в комплекте с гайками.
Крепеж: упрочненные Т-винты 80 мм + упрочненные винты для упоров.
Кабинет — самоделка.
Промышленный пылесос. В принципе, сейчас придумал кабинет без дна, в котором стружка будет ссыпаться в коробку сама, так что пылесос будет не очень нужен. Но до этого — покупал в каждое новое место, куда ставим станок, без пылесоса из кабинета стружку доставать шибко тяжело.
Этого набора вполне хватает в 99% случаев.
На этом разрешите откланяться, в следующий раз — немножко о софте, общие понятия обработки и стратегии обработки.
habr.com
Создание ‘ручного’ ЧПУ фрезера
При производстве 3D принтеров, да и вообще при создании многих вещей, иногда нам очень часто требуется фрезер для металла и прочих очень ‘вредных’ и сложных в ручной обработке материалов. Поэтому к нам пришла мысля :’А почему бы не…?’Начали мы с простого варианта, использовали дерево, 3D принтер и полированные валы. В итоге получили такое создание.

С его помощью мы смогли обрабатывать фанеру, бальзу и при малых скоростях оргстекло. Но проработал он довольно немного. Около 2-ух месяцев при загруженности 3-4 раза в неделю по 7-8часов. По итогу у нас расшатались стойки портала и валы начали люфтить по чёрному.
После небольшого мозгования, решили начать изготовление фрезера из листового металла 3мм.

Первая: для оси Х использовали полированные валы ⌀16 мм. После полумесяца работы и экспериментов было выявлено, что при такой длине валов усилие, при обработке алюминия, вызывает изгиб валов на середине вала. Это приводило к плачевным результатам обработки.
Вторая: валы оси Х были выполнены на рельсах. Рельсы смогли обеспечить необходимую жесткость для свободной обработки алюминия без ‘танцов с бубном’.
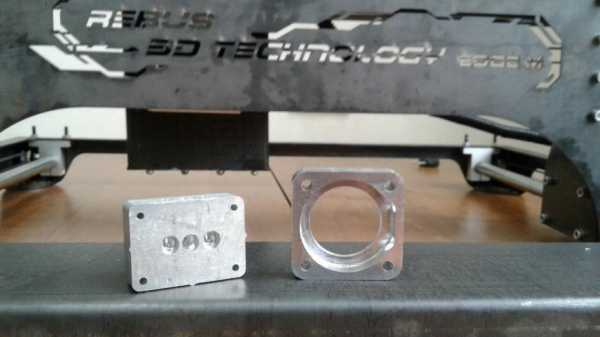
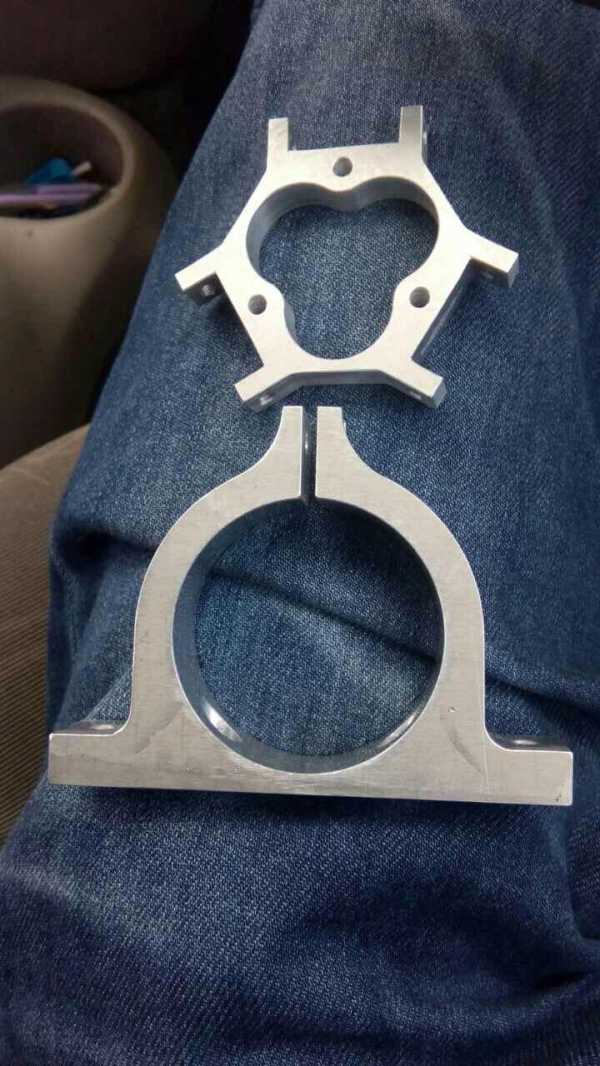

На днях проводили генеральную проверку и сервис нашего фрезера. Разбирали каретки и проверяли валы, смазывали направляющие, модернизировали гайку на оси Z.

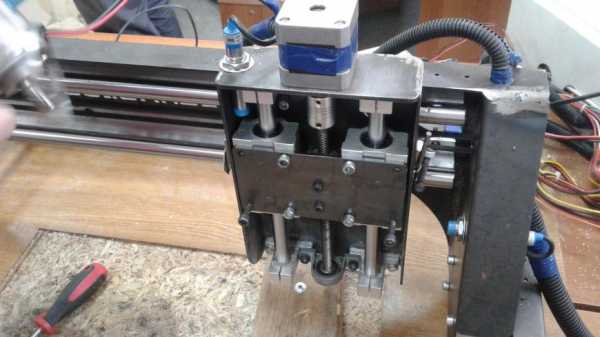
Есть уже разработанная новая конструкция в которой мы ушли от использования ремней и перешли на ШВП. Так же добавили металлический стол с Т-образными пазами под крепление оснастки.
Если останутся вопросы, или Вы заинтересовались нашими фрезерами, то напишите нам:
ВКонтакте;На почту.
3dtoday.ru
От ЧПУ Фрезера до 3д Принтера. Много фотографий. Длиннопост.
Все началось с идеи заполучить себе это волшебное (как я тогда думал) устройство. А как же различные корпуса, механика шестеренки и прочее, чего часто не хватает самодельщику)Будучи бедным студентом мои мечты долго оставались ими, но долгое время изучал тему в интернете, набирался теории и потихоньку волшебство техники из черного ящика плавно испарялось) Все становилось понятнее) Обсудив идею с отцом и его другом разговор плавно перетек с 3д принтера на его старшего брата — Фрезерный станок с ЧПУ) В итоге были выделены средства из семейного бюджета на его постройку как ожидаемый альтернативный источник дохода в наше неспокойное время)
Отец собрал всю механику а я всю электронику.
Процесс сборки:


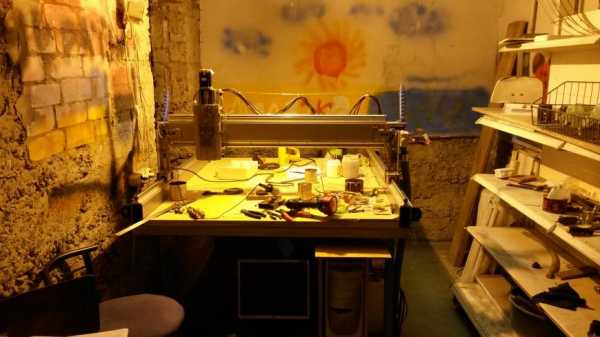
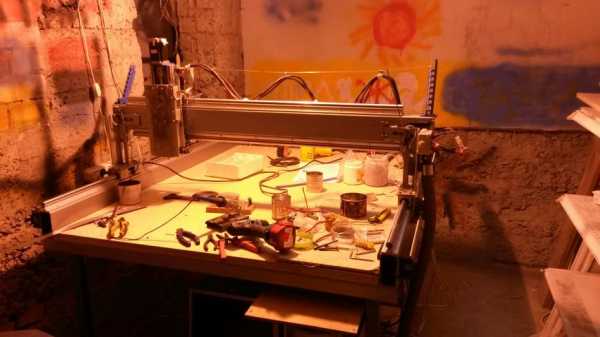
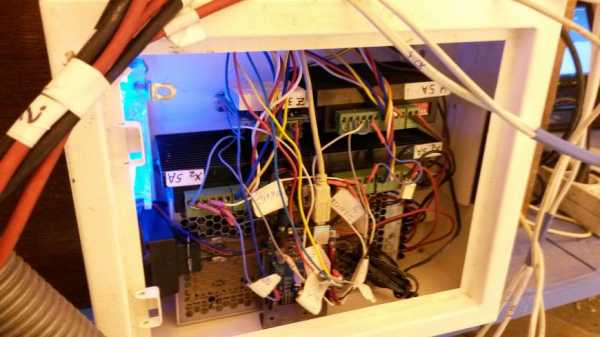





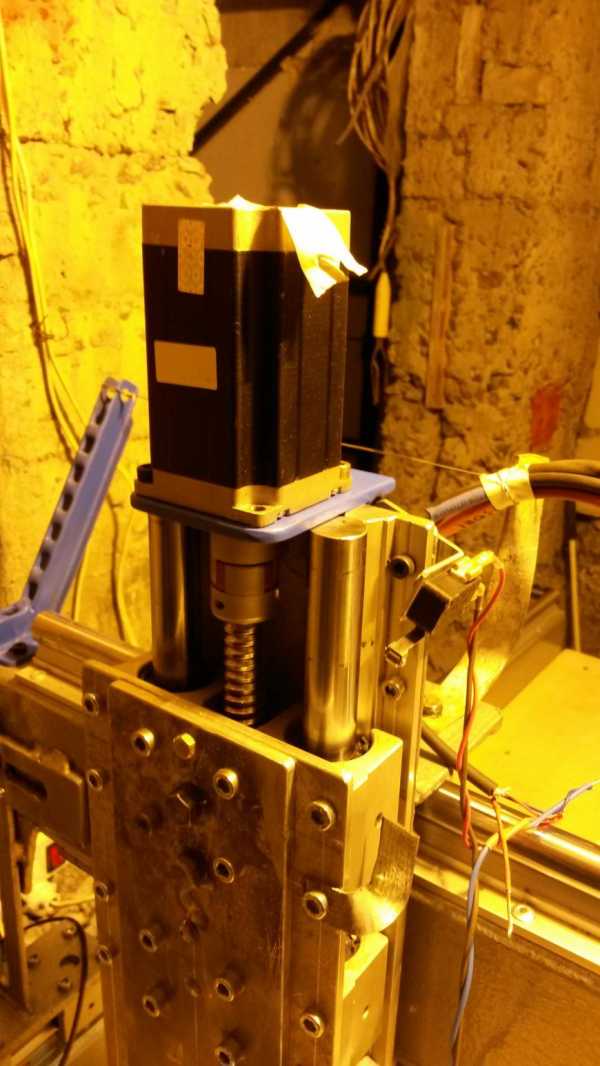
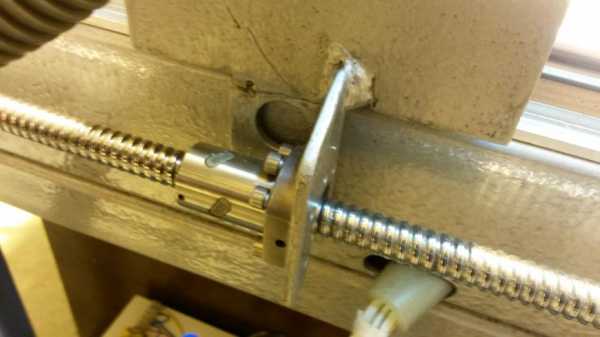
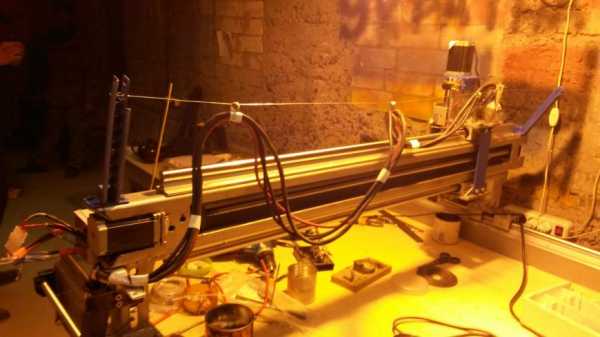







Впоследствии в Китае был куплен специальный для станков, Асинхронный с частотником и водяным охлаждением:



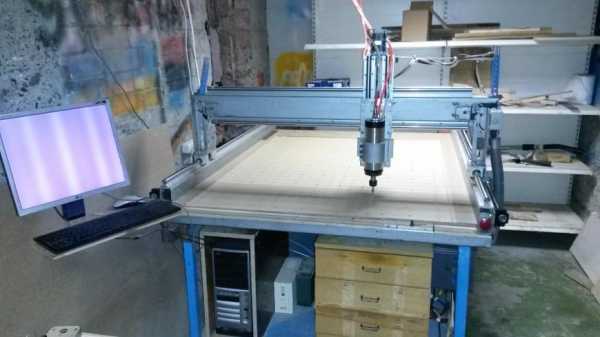
Но это уже другая история) переходим к 3д принтеру.
3Д ПРИНТЕР:
Детальки всего принтера были смоделированы в Солидворкс (хоть чему полезному в универе научили)
Експортировал в двумерный чертеж и открывал в Арткам (ЧПУшники поймут)
Вырезание:







Далее вставляем каретку оси z:
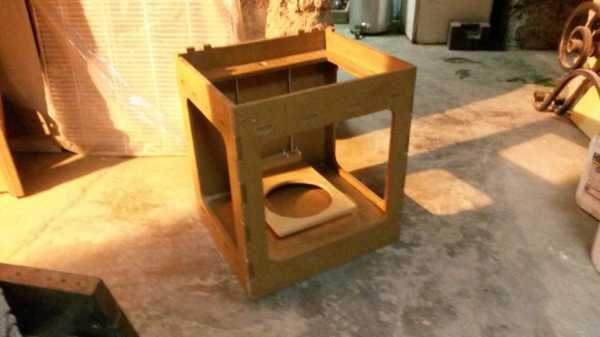


К тому же 2 двигателя на одной оси z приводят к еще одной популярной проблеме – воблинг. В общем я решил заранее уйти от этих проблем и выбрал компоновку со столом на оси z.
Валы 8 мм Подшипники запрессованы внутрь сборок из Двп.
Установка электроники:
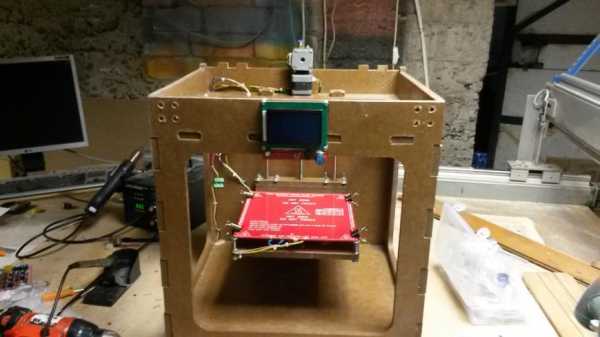




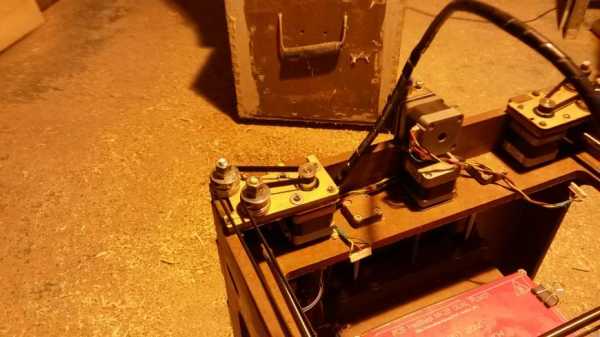






Первая печать:


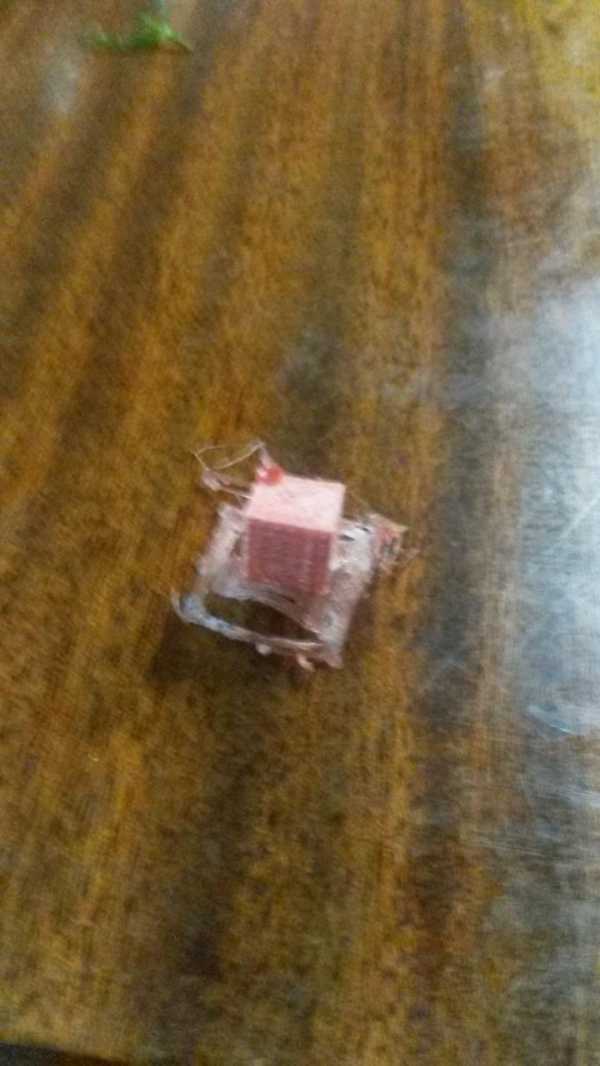




Прижим:
Сперва деревянный:



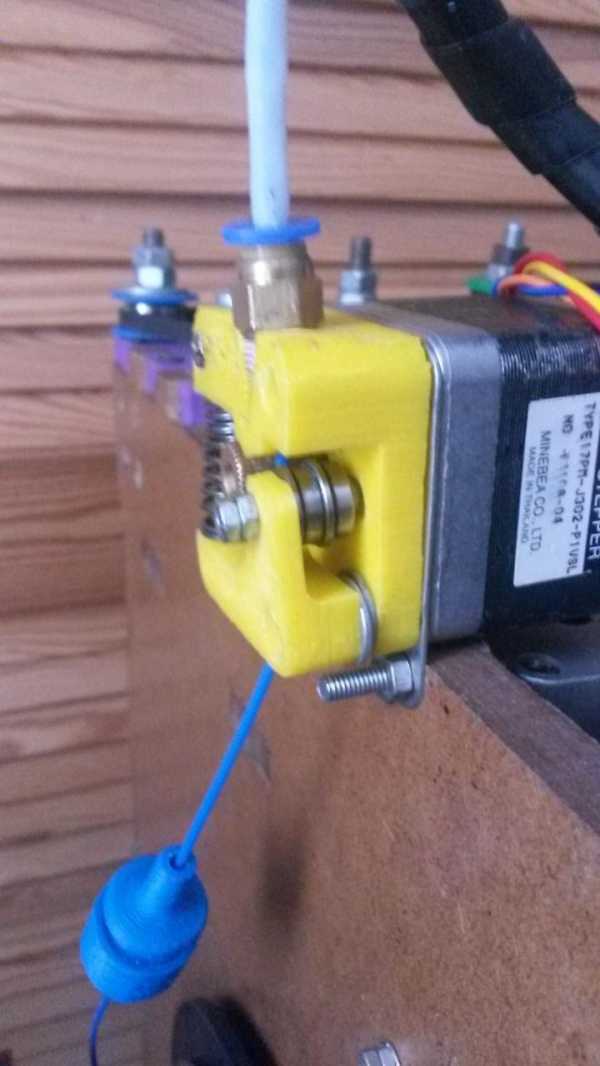



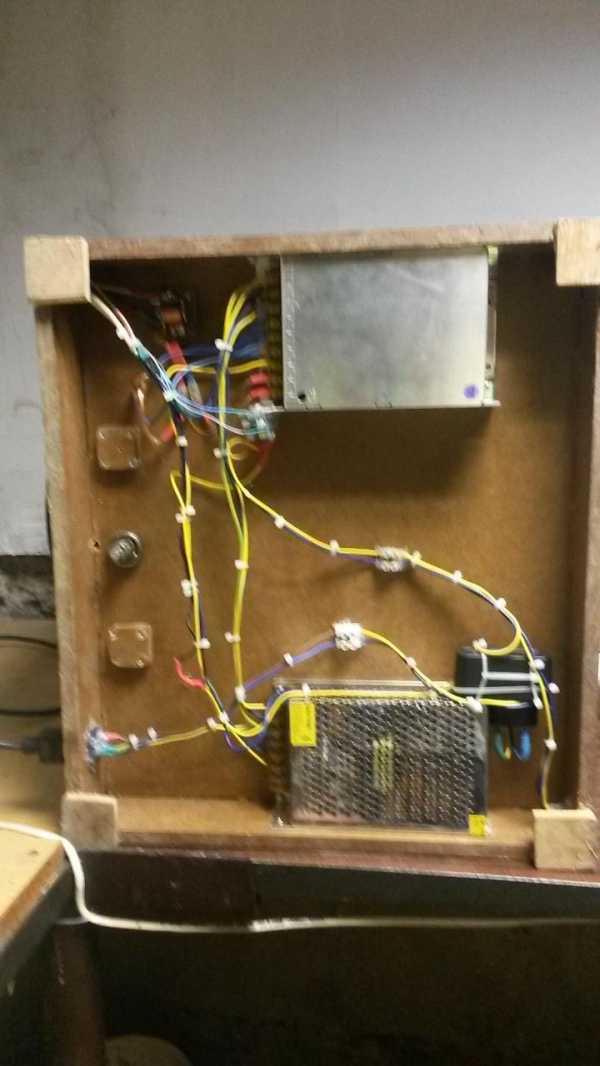
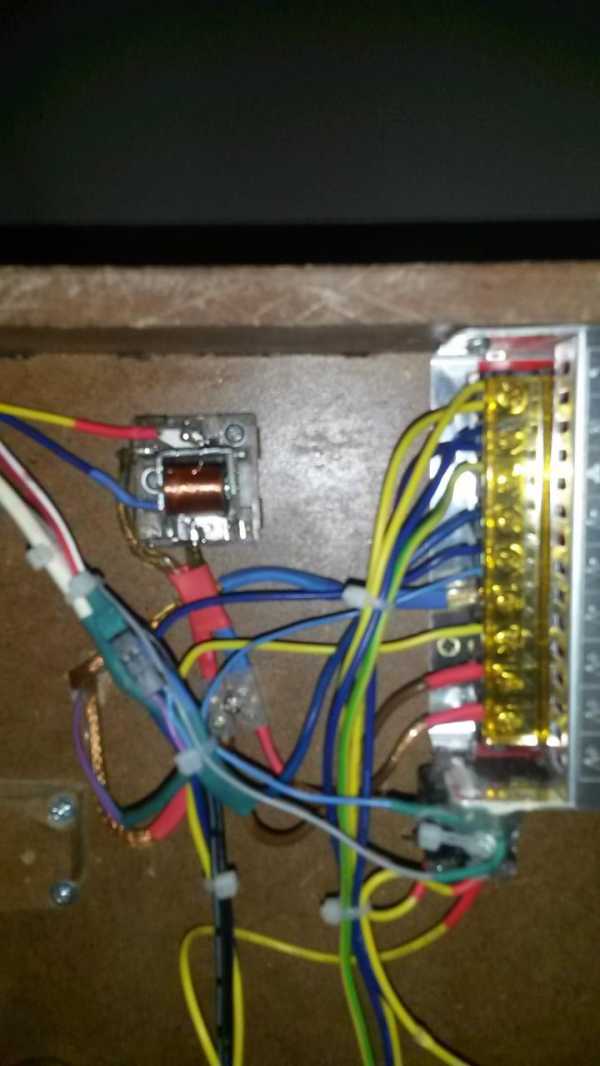





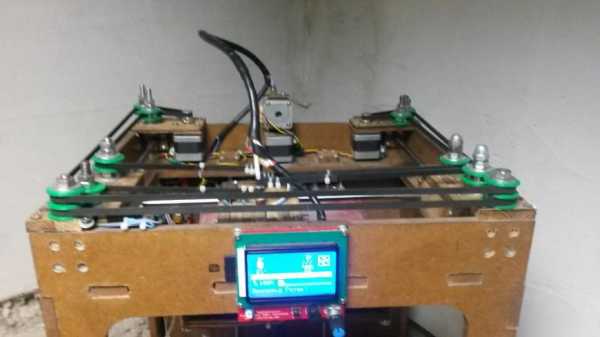




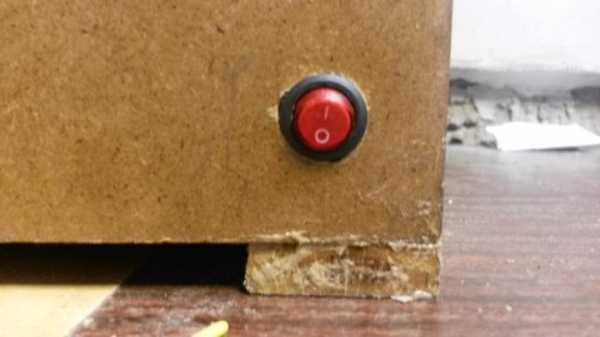


Печать котиков:


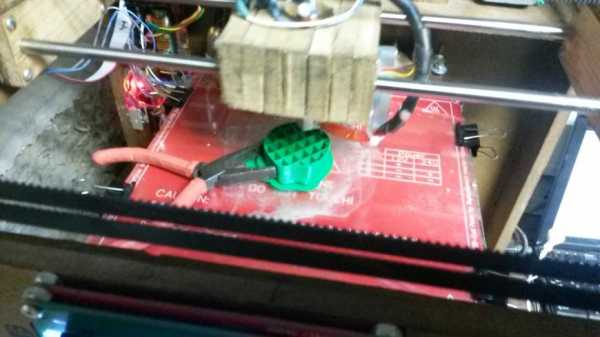


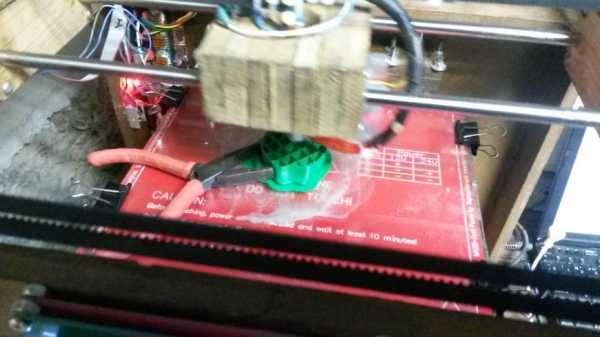


Со временем было проведено несколько крупных модернизаций:
Добавлены дверцы из оргстекла (выше можно увидеть его вырезание на ЧПУ):
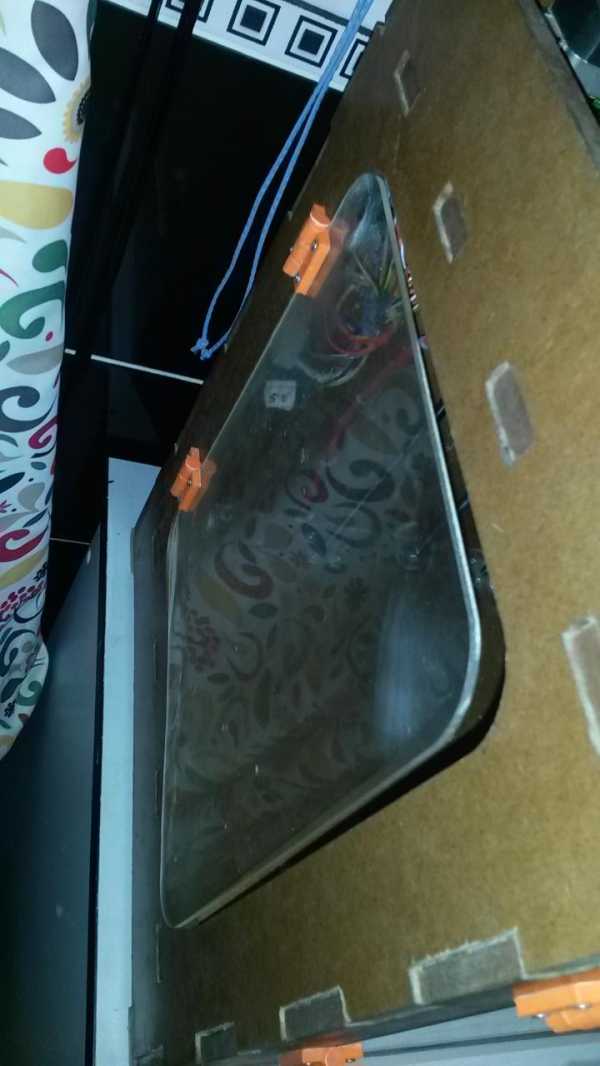






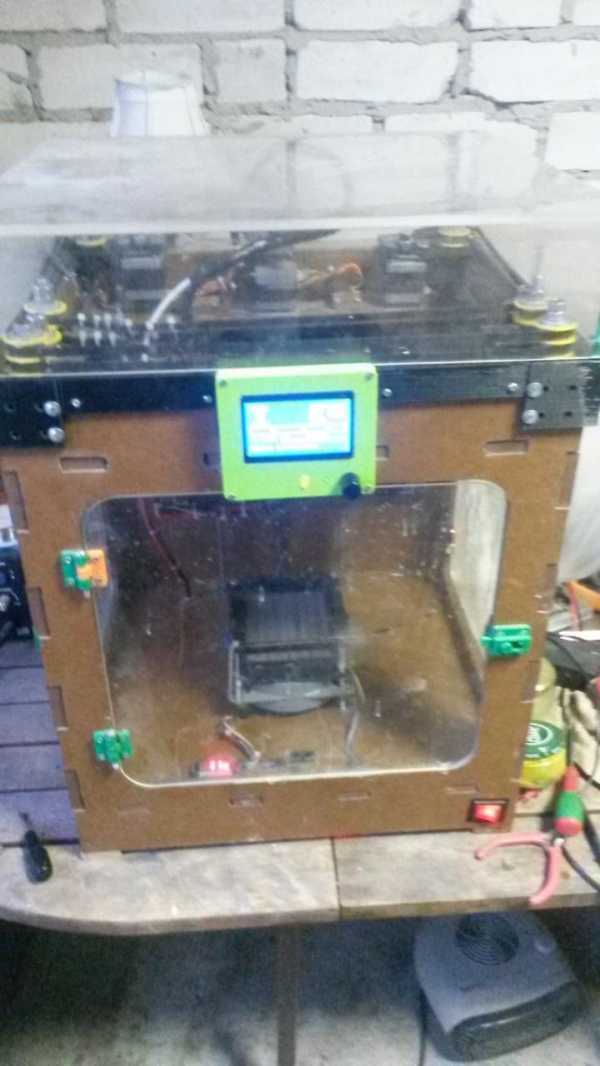

К стати лайфхак: На Рампс есть специальный пин для управления питанием (можно настроить в прошивке). Ардуино у меня работает от 5 вольт через отдельный БП (зарядка мобилы) и через этот пин управляет реле через транзистор. Это реле замыкает контакты 220в включая силовую цепь (блоки питания 12 вольт). Таким образом через кастомный G-Code M80 и M81 можно управлять силовым питанием. Тогда если прописать в слайсере эту команду (M81) в конечный G-Code то когда печать окончится принтер выключится (кроме экранчика и Ардуино). Кроме того при Срабатывании вотчдога и перезагрузке Ардуино а также любой другой неисправности Реле автоматически отключается и выключает принтер спасая от возможного пожара.
Практика показала что длинные сигнальные провода до дисплея (и СД карты) не приводят ни к чему хорошему в плане стабильности печати (особенно если рядом пролегают провода питания подсветки) Поэтому дисплей со временем был перенесен вниз:



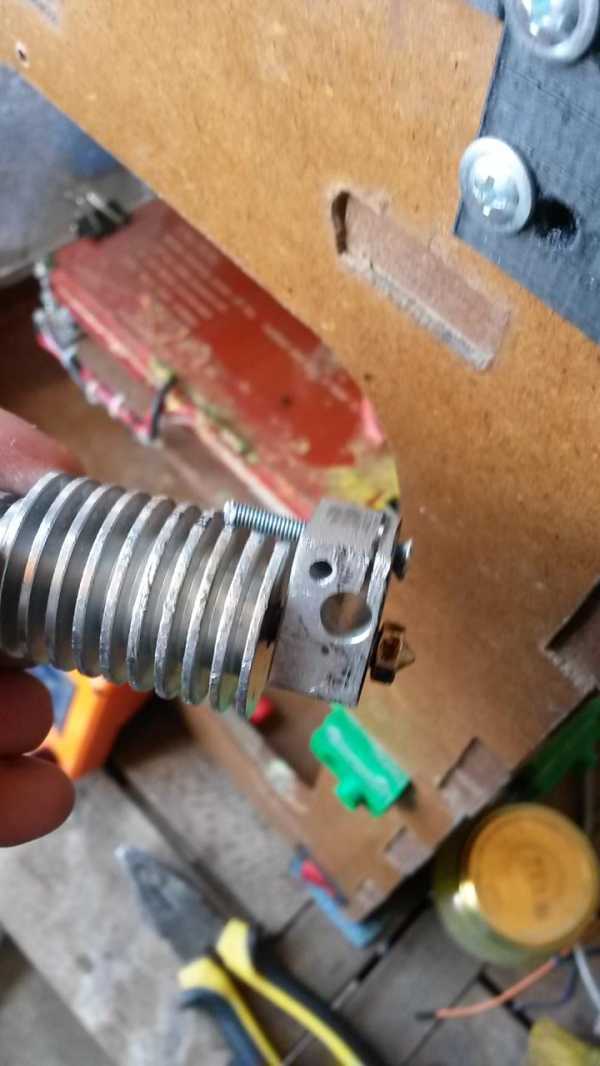

Обогрев немного уменьшил максимальную высоту печати (на 20 мм) но зато теперь можно печатать действительно крупные детали из дешевого АБС без расслоений:
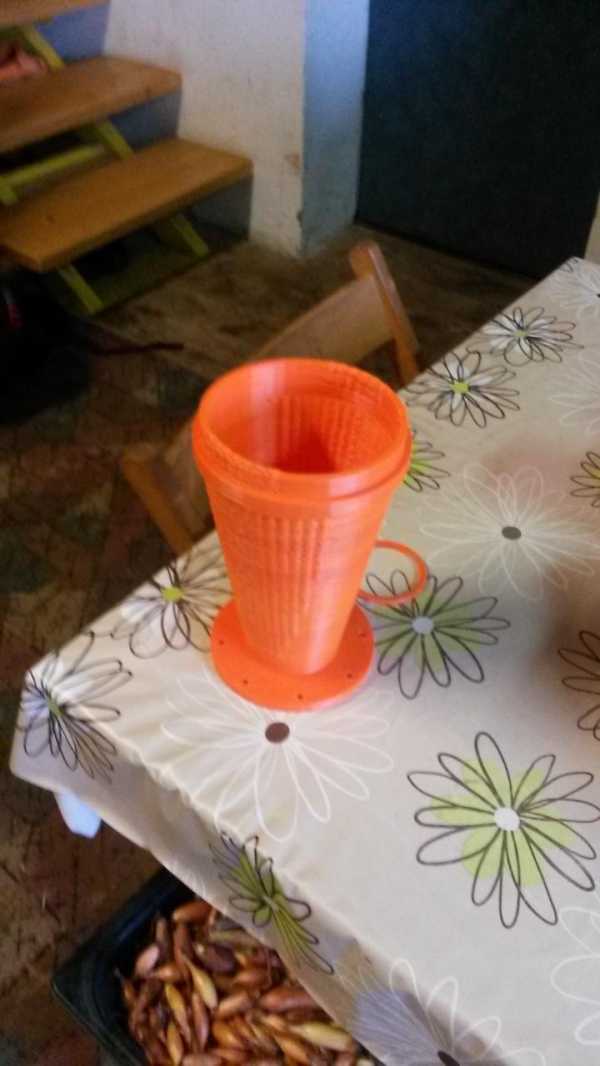
На сим окончим пожалуй этот пост уже весьма немалый) Но я не прощаюсь и в следующий раз расскажу о постройке Лазерного CO2 станка с ЧПУ с использованием этого принтера)
Ну а пока посмотрите что было напечатано:


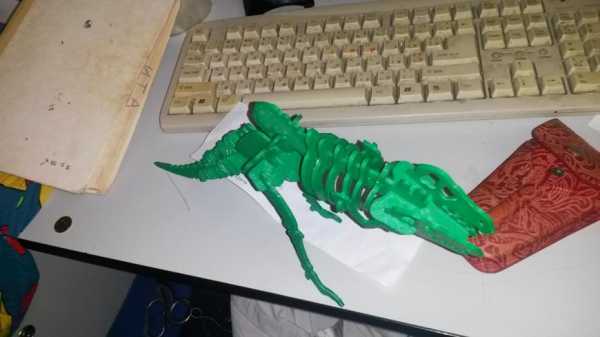



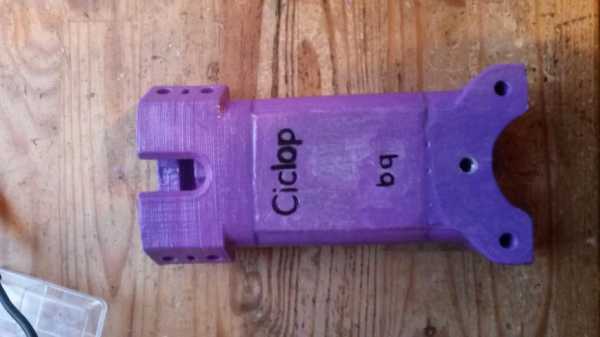
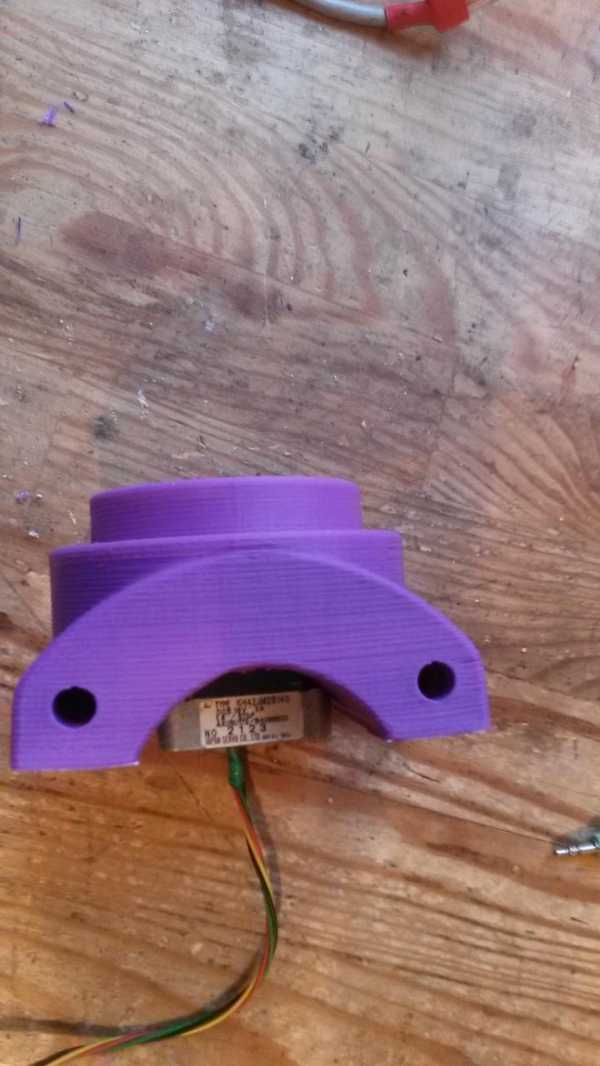
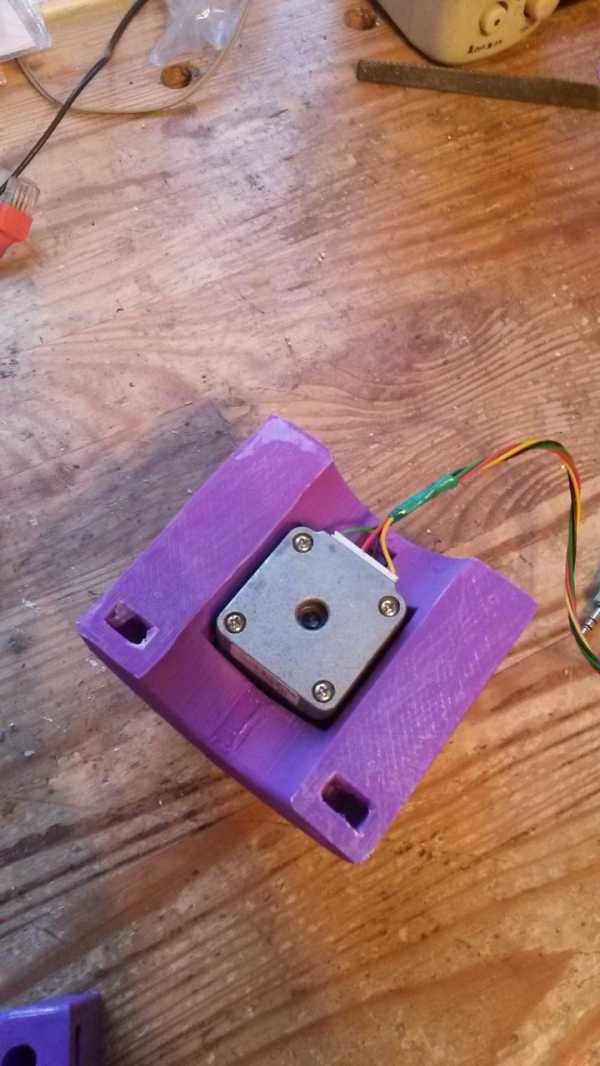
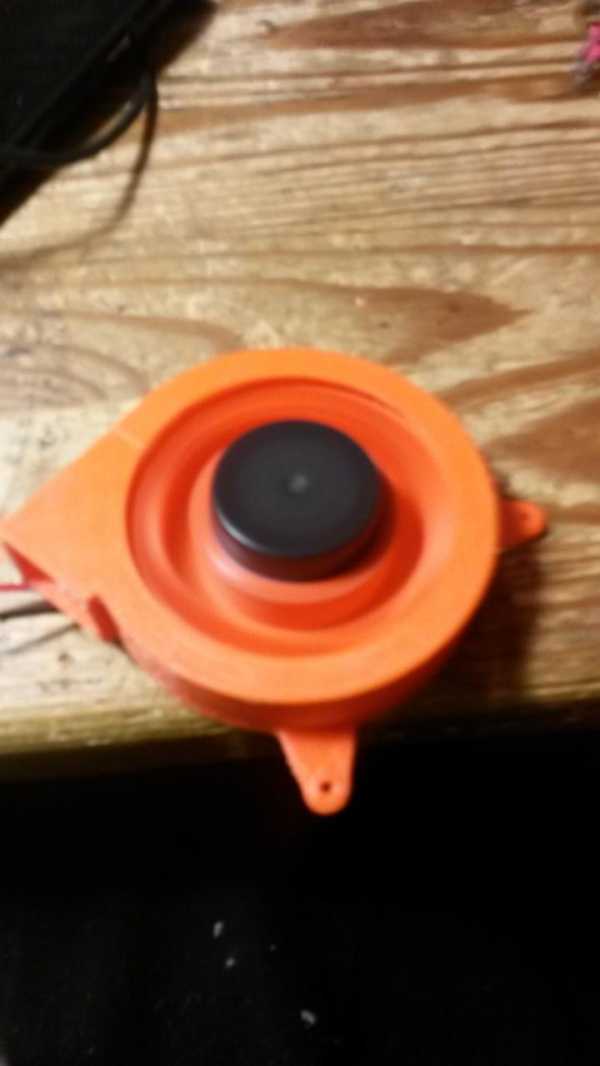


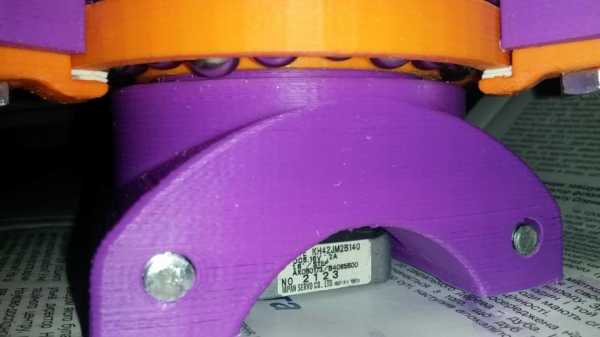

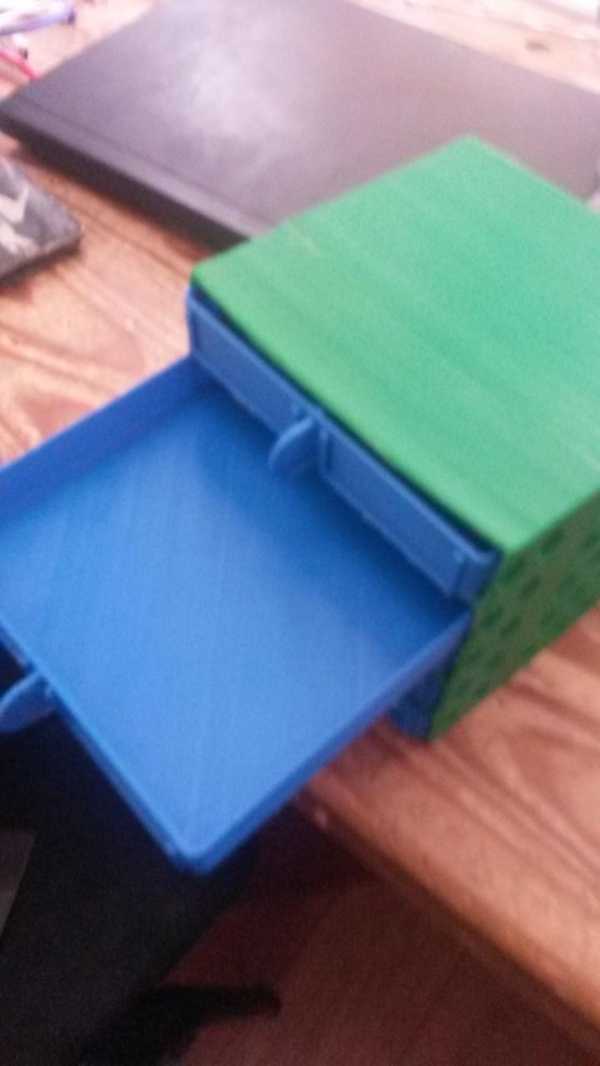




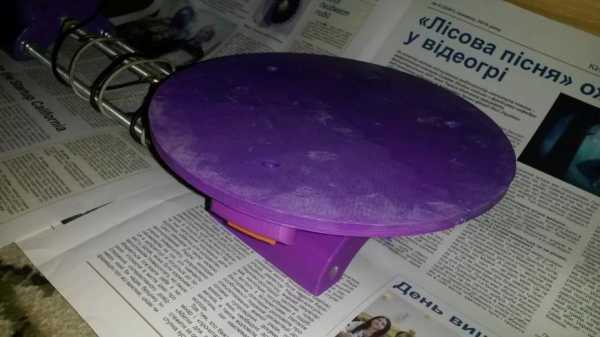

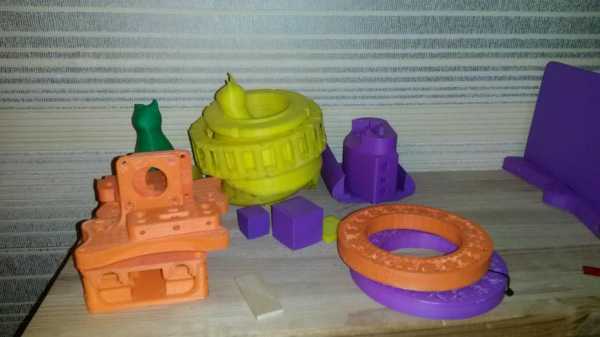
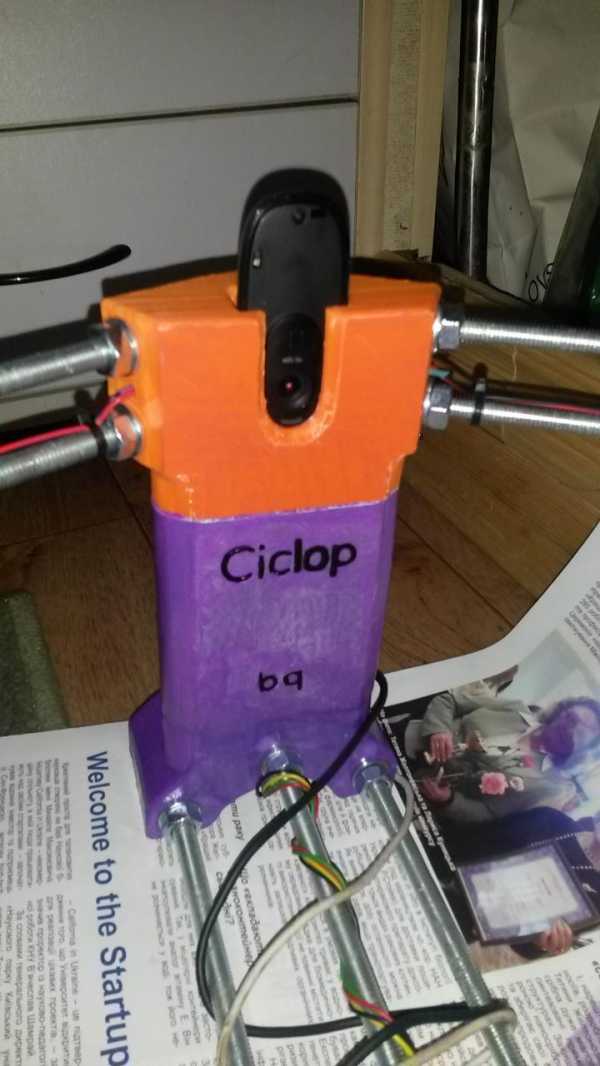




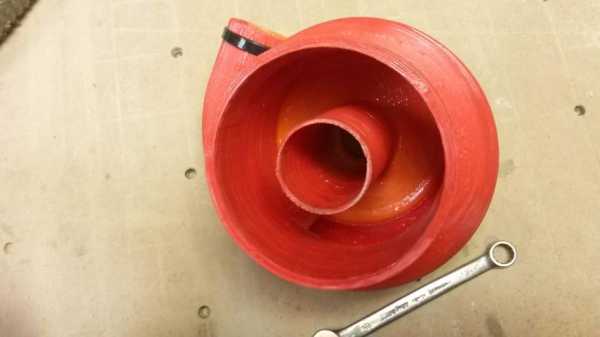
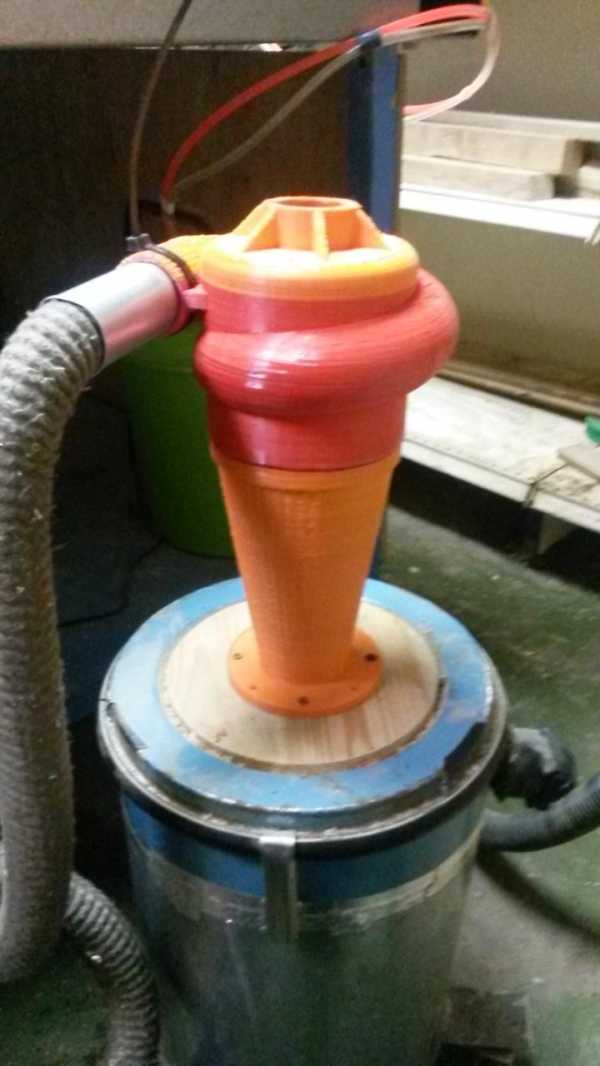











3dtoday.ru
Snapmaker — 3D принтер, лазерный гравер и фрезер с ЧПУ в одном станке
МЫ НЕ ЗАНИМАЕМСЯ ПОСТАВКОЙ ДАННОГО ОБОРУДОВАНИЯЗАКАЗАТЬ МОЖНО ТУТ: SNAPMAKER НА КИКСТАРТЕРЕ
ЦЕНА ПО РАННЕМУ ПРЕДЗАКАЗУ: $199 за 3D принтер. Дополнительные модули по $69 за каждый.

3D принтер — удивительная вещь! К сожалению, они массивны, сложны, дороги и имеют ограниченные функции и сложные настройки, причиняющие головную боль. Команда изобретателей из США решила изменить эту ситуацию и создала простой в использовании и доступный 3D принтер.

Конструкция Snapmaker разработана таким образом, чтобы обеспечить максимально удобную работу. Пространство рабочего стола позволяет сочетать функции 3D-принтера, лазерного гравера и ЧПУ со сменными головками.
Металлическая конструкция

Snapmaker полностью изготовлен из металла, что обеспечивает высокое качество и надежность работы. Аппарат использует цельнометаллическое шасси из алюминиевого сплава.
Модульный дизайн

Инновационная модульная конструкция делает возможной быструю сборку, расширенные дополнительные функции, снижает себестоимость и, как следствие, конечную стоимость оборудования. Использование плоской упаковки обеспечивает низкую стоимость доставки. Новый тип линейного модуля может использоваться в любом из X, Y, Z-направлений и отвечает за высокую точность линейного перемещения.
Высокая точность
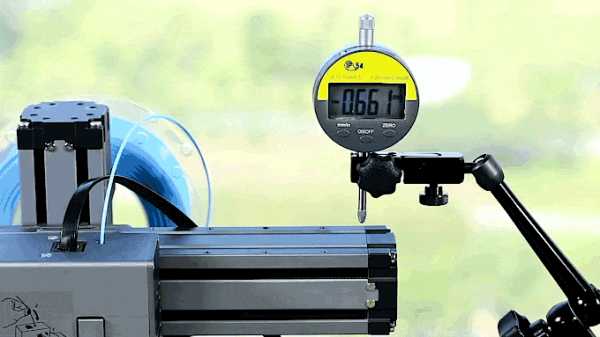
Ключом к высокой точности является сочетание прочной обтекаемой конструкции с системой управления ЧПУ. Snapmaker гарантирует высокое качество печати с отличной детализацией.
Высокое разрешение


Высокое разрешение 3D-печати теперь доступная реальность с Snapmaker. Он не уступает в качестве печати 3D принтеру стоимостью $1000.
Простота в использовании

Snapmaker поставляется с очень понятным и удобным программным обеспечением Snap3D. Просто перетащите в него файл, приготовленный для печати. Кроме Snap3D, вы можете использовать любое другое предпочтительное программное обеспечение.
Цветной сенсорный экран

Благодаря интуитивно понятному сенсорному экрану вы можете проверять и контролировать различные настройки, например, загрузку нити.
Авто-выравнивание

В отличие от большинства традиционных 3D-принтеров, Snapmaker не нужно выравнивать. Просто задайте Z-смещение оси кусочком бумаги и Snap3D, а затем наслаждайтесь 3D-печатью.
Легкость в сборке

Вы когда-нибудь собирали 3D-принтер за 10 минут? С Snapmaker это стало возможным! Легкая установка 10 частей всего за 10 минут. Это круто!
Лазерная гравировка

Snapmaker легко трансформируется в лазерный гравер с помощью 500 мВт лазерной насадки с длиной волны 405 нм и может быть использован для гравировки изображений и логотипов на древесине, пластике, бумаге, ткани, коже и т.д.
Фрезеровка ЧПУ

Snapmaker позволяет выполнять резьбу по дереву, акрилу, стеклотекстолиту при использовании дополнительного модуля ЧПУ. Фрезерный шпиндель развивает скорость от 2000 до 7000 оборотов в минуту.
Сменные модули предоставляют широкие возможности использования Snapmaker. Вместо покупки трех машин стоимостью около $500 за штуку, теперь вы можете использовать один компактный и надежный аппарат, экономя ваши деньги и место на рабочем столе.
В конфигурации 3D-принтера устройство способно выстраивать модели размером до 125х125х125 мм слоями от 50 до 300 микрон со скоростью позиционирования до 150 мм/с, используя сопло диаметром 0,5 мм. Рабочий столик прогревается до 100°С. Закрытый корпус не предусмотрен, но относительно небольшой рабочий объем должен позволить работать как с ПЛА, так и АБС, нейлоном, поливиниловым спиртом и другими филаментами диаметром 1,75 мм.
Передача данных осуществляется посредством USB соединения или кард-ридера Micro SD. В качестве программного обеспечения используется фирменный интерфейс Snap3D и различные слайсеры – Cura, Simplify 3D, Slic3r и др.
Конфигурации

www.stankoff.ru
Как выбрать фрезер с ЧПУ – практические советы
Станки с ЧПУ последнее время полностью оккупировали некоторые сферы производства, например мебельную и столярную отрасль. А то, что фрезерные работы при помощи этих станков просто замечательно получаются, делает их сверх популярными. Все предприятия, которые занимаются деревообработкой, обязательно имеют в своём арсенале эти замечательные станки. Также эти станки часто применяются и в других отраслях, в том числе и в отрасли производства рекламной продукции.
Вполне естественно, что сделать выбор такого станка непросто, ведь сначала необходимо изучить непростой ассортимент, который постоянно меняется. Часто случается так, что люди в спешке покупают станок, а затем обнаруживают в нём либо массу ненужных функций, за которые произошла переплата, либо же наоборот — недостаток этих функций. И тот и другой случай можно охарактеризовать как выброс денег. Существует ряд советов, которые можно дать новичкам в таком нелегком выборе.
Сперва выделим основные черты, на которые необходимо обратить своё внимание при выборе какой-либо модели фрезерного станка. Для начала попробуйте выделить основные задачи. Также было бы неплохо суметь заглянуть немного вперёд и выбрать станок с небольшим запасом задач. Необходимо готовиться к будущему расширению своих возможностей прямо сейчас. Попробуйте действовать исходя из размеров возможных обрабатываемых заготовок. По этой информации Вы сможете рассчитать рабочую зону, а соответственно и выбрать модификацию станка, если, конечно же, станок может выбираться в вашем случае только по этому критерию. Зато Вы полностью сможете обработать деталь за один цикл работы фрезы.
Внимательно изучите принципиальную схему и конструкцию станка
Также хорошо рассмотрите портал — он должен быть сделан из толстой стали, которая одновременно играет роль станины и не даёт заготовке вибрировать, а следственно и деформироваться. Порталы из алюминия являются результатом жадности производителей, потому что они недостаточно прочные и могут как сами выйти из строя, так и повредить деталь или же сам инструмент. Также достойна внимания величина ходя шпинделя по вертикальной оси, что практически является показателем толщины обрабатываемой детали. Так, например, если длина шпинделя составляет 300 мм, то вполне может быть, что при вычитании длины патрона мы получим всего 120-140 миллиметров толщины обрабатываемой детали, то есть примерно половина длины шпинделя.
Шпиндель
Выбор электрошпинделя также не требует наличия специальных знаний, потому что это едва ли не самая не прихотливая часть фрезерного станка с чпу. Шпиндель фрезерного станка оснащен жидкостным охлаждением, что позволит обеспечить работу станка в круглосуточном режиме. На ряду с жидкостным охлаждением шпиндели более высокой мощности от 3кВт оснащают воздушным охлаждением. Качественный шпиндель при ежедневных нагрузках и грамотном уходе может прослужить не много не мало, а как минимум 5 лет, учитывая то, что в России для вышеперечисленных производителей есть центры обслуживания, где всегда проведут ремонт или профилактику для любого шпинделя. Выбор шпинделя по мощности необходимо делать с некоторым запасом, хотя бы в 10%.
Двигатель перемещения
Всего можно выделить два типа таких двигателей по типу перемещения — либо шаговый вариант, либо серводвигатели, которые куда более быстрые и точные, потому что они не имеют такой особенности, как суммация погрешностей в процессе непрерывной работы. У них нет такого неприятного явления как пропуск шага, который постоянно возникает на всех шаговых двигателях. Серводвигатели — устройства сложные, поэтому здесь также необходимо выбирать производителя, который проверен профессионалами на безотказность — так, например, это может быть Panasonic, Yaskawa, Delta. Эти имена должны подарить вам должную надежность и точность.
Количество инструмента
Сразу продумайте всё так, чтобы количество инструмента, который необходим для резки, было выбрано с запасом. Бывает такое, что в результате просчёта инструмента не хватает, чтобы изготовить даже одну деталь. Поэтому необходимо рассматривать варианты, когда количество инструментов достаточно велико, но при это можно выбрать станок, которые будет менять инструмент в полуавтоматическом или автоматическом режиме, что очень удобно.
Стойка управления
Внимательно просмотрите все возможности стойки управления вашим будущим станком. Самый лучший производитель безотказных стоек — это Syntec, который производит своё оборудование в Тайване. Стойки от этой фирмы уже полностью являются законченным продуктом, который не требует установки персонального компьютера, а если перечислять все преимущества этих стоек, то тогда не хватит никакой статьи.
Програмное обеспечение
Постарайтесь заранее ознакомиться с программным обеспечением, которое будет идти вместе со станком. Обычно с ними поставляются Type3. Кроме того, учтите что интерфейс будет на английском языке.
Обслуживание станка
Это одна из самых важных сторон, на которые необходимо обращать внимание в первую очередь, иначе Вы рискуете провести всё свое время с инструкцией и набором отвёрток самостоятельно над нерабочим станком. Развитая сервисная служба — это залог ваших спокойных нервов, тем более, что при покупке Вам полностью помогут сделать монтаж и отладку этого оборудования прямо на месте. Также обращайте внимание на то, чтобы компания, которая будет Вам продавать станок, действительно имела связи с сервисным центром. Обычно же сервисные центры, которые имеются при таких компаниях, имеют низкое качество обслуживания, а квалификации у персонала нет, откровенно говоря, никакой. Можно махнуть рукой на наши рекомендации, но представьте хотя бы на минуту, что может стать производство, а псевдоспециалисты не смогут Вам помочь. Поэтому не нужно ориентироваться при покупке только лишь на низкую стоимость товара — она своё ещё отработает в обратную.
Если же даже после большого количества столь дельных советов Вам оказалось достаточно трудно сделать выбор, то в таком случае обращайтесь за консультацией к профильным специалистам, которые легко помогут подобрать станок, который максимально будет соответствовать вашим нуждам. Оборудование лучше всего смотреть в выставочном или демонстрационном зале, а также на действующем производстве, где уже работают такие станки.
Компания Формат вот уже в течение большого количества лет занимается поставками фрезерных станков с ЧПУ. Также у нас хватает опытных специалистов, которые быстро производят подбор или же наладку оборудования в кратчайшие сроки. Такие станки — это многосложные системы, поэтому если у вас нет соответствующего опыта, то лучше обратиться к консультантам за помощью.
Основные направления использования фрезерных станков с ЧПУ это изготовление следующих типов изделий:
- корпусная и цельная мебель, такая как мебель для кухни, различные варианты компьютерных столов, мебель для офиса, мебель для торговли и выставок, шкафы-купе и т. д.)
- мебельные фасады, а также декоративные элементы мебели, как из цельного дерева, так и из композитных материалов
- двери, а также всевозможные аксессуары к ним (наличники, пороги, ручки)
- гравированный паркет, декоративная резьба по дереву, а также узоры на фанере
- художественного паркета и декоративной резьбы
- моделирование форм и болванок для процесса литья
- многочисленная продукция для рекламной отрасли, а также изготовление сувениров и подарков
infofrezer.ru